Operational excellence dankzij Six Sigma data-analyse: Tata Steel dóet het
Tata Steel produceert, bewerkt en distribueert hoogwaardig staal voor producten die het leven vergemakkelijken. Het is een bedrijf van Nederlandse bodem waar wij bijzonder trots op mogen zijn. Het is namelijk het op vijf na grootste staalconcern ter wereld. Sander van Campen is senior improvement consultant bij de afdeling BEX van Tata Steel. “BEX staat voor business excellence en heeft operational excellence als belangrijkste doel. Daarvoor richten mijn collega’s en ik ons op drie pijlers, namelijk daily management, continuous improvement (het maximale halen uit huidige processen) en innovatie. Ik richt me vooral op continuous improvement. Een geweldige tak van sport, omdat ik mij bezig mag houden met probleemoplossen volgens de Six Sigma methodiek. En daar komt ook Symbol om de hoek kijken.”
Six Sigma-projecten door Tata Steel Green Belts
Symbol leidt Tata Steel medewerkers op als Green en Black Belt, helpt bij de projectbegeleiding als er capaciteitsproblemen zijn en draagt zorg voor de certificering via de LSSA. “De inhoudelijke training wordt door Symbol verzorgd, zelf pakken wij het praktijkgedeelte en de begeleiding van de projecten, op”, vertelt Van Campen, zelf door Symbol opgeleid als Black Belt. “De projecten van deze Green Belts zijn vaak al behoorlijk complex: er worden in projectteams KPI’s aangepakt die niet voldoen aan de specificaties en waar snel een verbeterslag op gemaakt kan worden. Het oplossen van een quality delivery probleem voor een klant bijvoorbeeld, of het op tijd beschikbaar hebben van materialen voor een campagne voor een bepaalde productsoort. Natuurlijk werken we ook met enabler projecten – met impact op het gebied van milieu en/of veiligheid – maar over het algemeen hanteren we de regel dat een project een positieve business case moet opleveren om uitgevoerd te mogen worden. Voor certificering moet een project moet op jaarbasis minimaal een besparing van 20.000 euro opleveren. De interne business cases zijn vaak hoger.”
Data driven projecten
Tijdens dit soort projecten worden de Green en Black belts gecoacht door Van Campen en zijn collega’s. “Dat is niet alleen om te zorgen dat de projecten goed blijven lopen, maar ook om te helpen met data analyses. Green Belts krijgen namelijk nogal wat voor hun kiezen wat betreft data analyse. Vrijwel al onze projecten zijn data driven. Daarom maken we tegenwoordig ook gebruik van advanced analytics, wat betekent dat we met geavanceerde modellen naar hele grote datasets kijken. Ik heb het dan over datasets vanaf vijftien variabelen of meer, bestaande uit minimaal 100.000 datapunten. Dit soort datasets komen binnen Tata Steel steeds vaker voor.”
Data lake in de cloud
“Het is ook één van de redenen dat onze IT-organisatie aan een data lake in de cloud werkt”, gaat Van Campen verder. “Binnen Tata Steel zijn inmiddels een paar honderdduizend tabellen beschikbaar waar data in zit. Die worden straks op één plek, in de cloud, netjes gecentreerd, zodat de data daar voor iedereen te vinden is. Dat gaat ons veel voordeel opleveren, want nu is die data decentraal verspreid over verschillende systemen. Concreet betekent dit dat Green Belts bij de start van een nieuw project de beheerders van de tabellen om toestemming moeten vragen. En dan moeten zij er met hun projectteam ook nog eerst achter komen welke data ze nodig hebben, waar die data staat en dus welke beheerder om toestemming gevraagd moet worden. Omslachtig, zeker gezien de grote hoeveelheid projecten die wordt opgepakt.”
Projecten met Six Sigma data-analyse
Alleen al de afgelopen tijd zijn er een flink aantal projecten uitgevoerd waarin Six Sigma data-analyse is ingezet. Die projecten zijn verweven in de jaarplannen en de overall doelstellingen van het MT, of ontstaan ad hoc. “Eén projectteam heeft bijvoorbeeld gekeken naar het transport van ruw ijzer naar de staalfabriek. Dat transport gebeurt in een ijzermenger, een soort torpedo die over het spoor vervoerd wordt en die vervolgens geleegd wordt. Tijdens het legen bleef structureel een deel van het ijzer zitten. Sinds het project wordt de ijzermenger effectiever geleegd. Per menger levert dat 1,3 procent meer ruwijzer op, wat op jaarbasis meer dan 200.000 euro opbrengt. Maar ook de doorlooptijd bij het invoeren van een staalrol in de koudbandwals is door een Six Sigma-project verbeterd. Er is een tijdwinst van vijf seconden gerealiseerd. Dat klinkt misschien niet veel, maar door het grote volume dat wij draaien betekent vijf seconden toch enkele tienduizenden euro’s aan besparing. Kortom: Six Sigma-projecten leveren Tata Steel écht veel op. En er komt steeds meer data beschikbaar en de kwaliteit van die data verbetert. Ik ben erg nieuwsgierig naar wat de toekomst ons gaat brengen.”
Continu verbeteren voor operational excellence
Natuurlijk is het wel van belang dat de medewerkers in de projectteams goed opgeleid zijn. En zoals eerder geschreven gebeurt die opleiding deels door Symbol. “De trainingen zijn uitgekristalliseerd en van een goed niveau. Heel werkbaar ook, want we hebben de training getataïseerd, zoals wij dat noemen. Oftewel: we hebben samen met Symbol gekeken hoe we de algemene theorie konden vertalen naar voorbeelden binnen onze organisatie. Daardoor zijn de trainingen herkenbaar voor onze medewerkers, en zijn de resultaten erg goed. Dat moet ook, want wij hebben als doelstelling dat uiteindelijk iedereen die binnen één van onze werkeenheden een managementrol heeft, minimaal Green Belt getraind moet zijn. Continu verbeteren is immers een belangrijk onderdeel van operational excellence, en je moet goed opgeleid zijn om dat aan te kunnen sturen én in je dagelijkse werk toe te kunnen passen.”
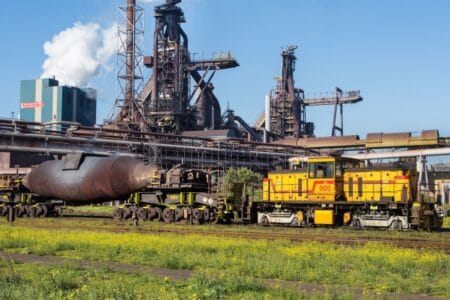
IJzermengers Tata Steel (bron: Tata Steel, Internet)
Laatste nieuws/blogs
Nederlandse productiviteit daalt opnieuw – en dat biedt juist kansen
De arbeidsproductiviteit in Nederland is opnieuw gedaald. Maar achter deze cijfers schuilt ook een kans: voor organisaties die bereid zijn slimmer te werken. In deze blog lees je welke structurele verbeteringen écht effect hebben – en waarom AI, rust en focus daarbij onmisbaar zijn.
Hoe vergevorderd is Continu Verbeteren in Nederland?
Hoe effectief is continu verbeteren in Nederlandse organisaties? Symbol onderzocht de grootste uitdagingen en succesfactoren. Ontdek hoe jouw organisatie scoort en welke stappen nodig zijn.
Snel lanceren zonder fouten
Wil je je product sneller en foutloos op de markt brengen? Met Design for Six Sigma (DfSS) verkort je de Time to Market en voorkom je fouten in de ontwerpfase.