Een junior consultant als tijdelijke extra kracht? Climax Molybdenum raadt het aan
“Net als verschillende collega’s heb ik naar volle tevredenheid een training bij Symbol gevolgd – in mijn geval was dat Lean Six Sigma Black Belt. Toen we een tijdelijke proces engineer nodig hadden, was mijn eerste gedachte dan ook om eens bij Symbol naar de mogelijkheden te informeren.” Aan het woord is Dirkjan Kooijman, senior process engineer bij het Rotterdamse Climax Molybdenum – onderdeel van het Amerikaanse Climax Molybdenum Company. In de fabriek in de Botlek wordt geconcentreerd molybdeenerts verwerkt tot molybdeenproducten die zowel in de industrie als in het dagelijks leven gebruikt worden. Enkele voorbeelden: auto’s, bruggen en zonnepanelen.
Een flink capaciteitsprobleem
Dirkjan vertelt verder: “Ons team bestond uit twee process engineers en we waren op zoek naar een derde collega.
Toen één van de engineers een andere baan kreeg, ontstond er dus een flink capaciteitsprobleem.
Normaal gesproken werken we veel met studenten van TU Delft, maar nu hadden we iemand met meer ervaring nodig om de periode naar een nieuwe vaste collega te overbruggen. Door mijn contactpersoon bij Symbol werd Hans naar voren geschoven, en dat bleek een goede match.”
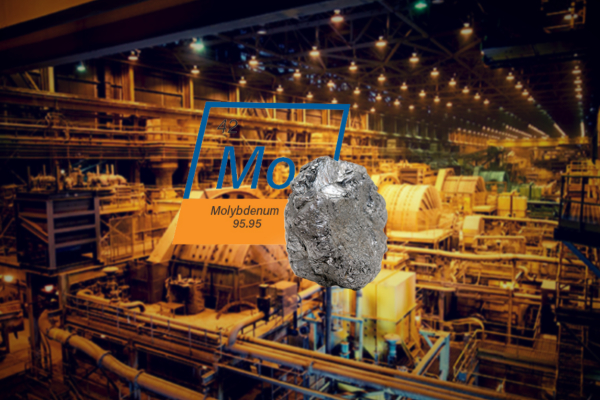
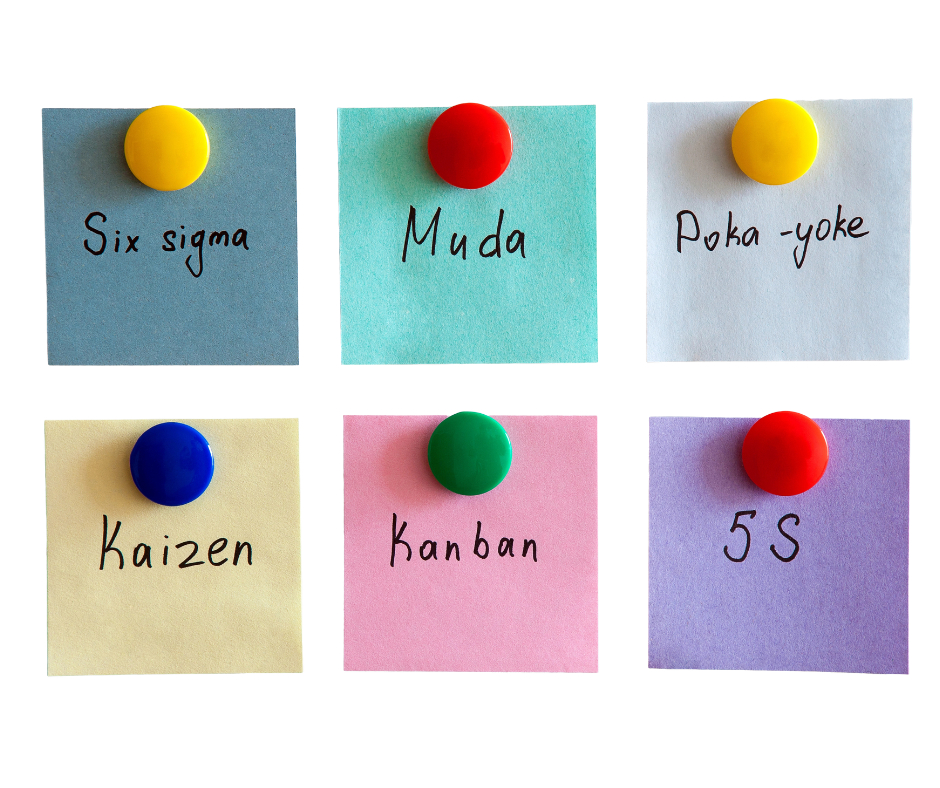
Systematisch aan de slag met Lean Six Sigma
Normaal gesproken werken nieuwe process engineers bij Climax Molybdenum eerst een half jaar mee in de ploegendienst, om zo kennis te krijgen van de specifieke productieprocessen. Voor Hans als tijdelijke kracht was zo’n uitgebreid inwerktraject natuurlijk niet mogelijk.
Dirkjan: “Hij werd in het diepe gegooid, en dat was voor hem soms best uitdagend. Maar door zijn systematische aanpak – die natuurlijk ook kenmerkend is voor Lean Six Sigma – was hij tóch snel in staat om projecten op te pakken en tot een goed resultaat te brengen.”
Oplossing voor in-line kwaliteitsmonitoring
Eén van die projecten had te maken met in-line kwaliteitsmonitoring. “Voorheen werd iedere dag één sample van een molybdeenproduct naar het laboratorium gestuurd om de deeltjesgrootte en dus de kwaliteit te meten. Dat had twee nadelen: de analyse duurde erg lang en bovendien kwam de uitslag altijd te laat. Als aan het einde van de dag bleek dat de kwaliteit niet voldeed, konden we geen instellingen meer wijzigen om toch aan de specificaties te voldoen. Om op tijd bij te kunnen sturen, wilden we met een in-line sensor continu de kwaliteit gaan monitoren. Die sensor hadden we al geïnstalleerd, maar we liepen nog tegen wat uitdagingen aan.”
Een goed werkend meetsysteem
Hans vult aan: “De data uit de sensor en de data uit het lab mochten natuurlijk niet (te veel) afwijken. Anders zou deze nieuwe manier van kwaliteitscontrole voor klanten immers niet acceptabel zijn. Door heel veel metingen uit te voeren, de uitkomsten steeds te vergelijken met de daadwerkelijke meetwaardes gemeten op het lab en aan de hand daarvan kalibraties uit te voeren, is het gelukt om de data uit de fabriek en het lab aan te laten sluiten. Oftewel: de sensor meet nu betrouwbaar. Ook heb ik de instellingen van de sensor verbeterd, zodat een paar praktische problemen – denk aan het verstopt raken van de sensor – zijn opgelost.”
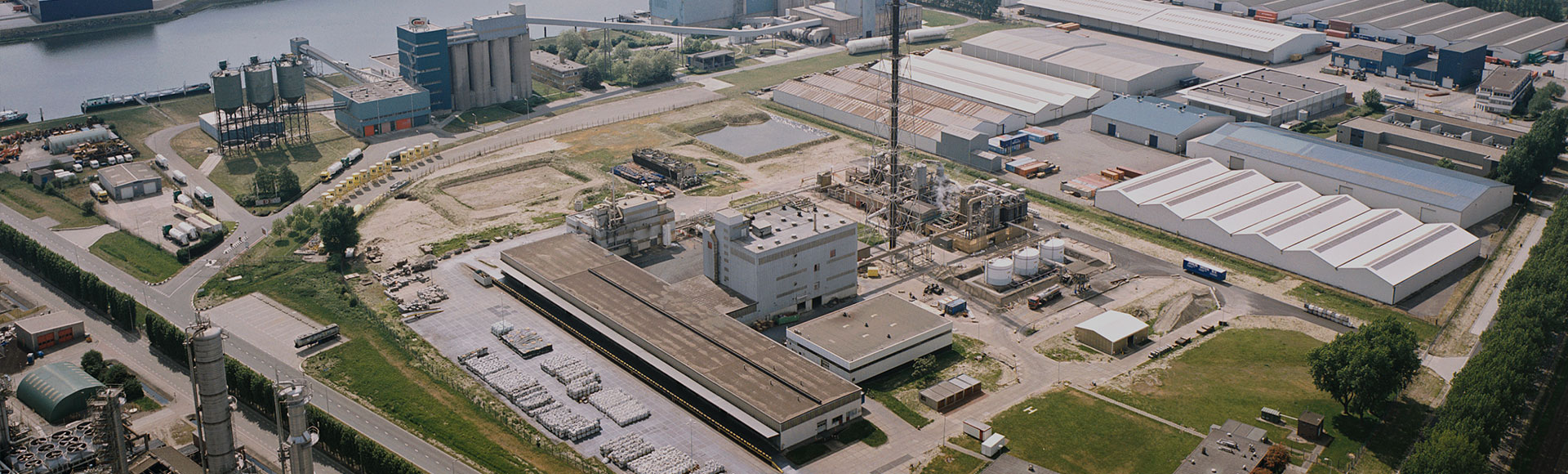
Online simulatieprogramma voor operators
Naast dit project heeft Hans nog een stuk of vijf andere projecten opgepakt. Hij vertelt: “Soms was ik chemicus, de andere keer consultant of zelfs financieel medewerker. Ik ben breed ingezet, en dat maakte het werk voor mij erg interessant.
Zo heb ik ook een investeringsvoorstel en een implementatieplan geschreven voor een nieuw opleidingsprogramma voor de operators.
Om de opleidingstijd te verkorten en het kennisoverdrachtproces te verbeteren, is in samenwerking met een bedrijf gespecialiseerd in software voor online trainingen een set digitale tools aangeboden die dit kunnen verwezenlijken.
Het gaat om kostbare software, maar met grote voordelen. Operators kunnen hiermee namelijk van achter hun computer standard operating procedures oefenen, met simulaties van hoe het er in de fabriek daadwerkelijk uitziet. Fouten maken is hierbij geen enkel probleem.
De plannen die ik heb geschreven om akkoord te krijgen, zijn inmiddels ingediend bij het hoofdkantoor in Amerika. Door in de fabriek mee te lopen in de ploegendienst, heb ik verder prio’s gemaakt in de werkinstructies die straks in ieder geval in de software geïmplementeerd moeten worden.”
Meters maken
Na iets minder dan een jaar zat Hans’ tijd bij Climax Molybdenum erop. Meerdere projecten – waaronder de twee genoemd in deze referentie – zijn in die tijd succesvol afgerond. Dirkjan: “Het is voor ons dus heel waardevol geweest om een junior consultant van Symbol in te schakelen. Zonder de tijdelijke hulp van Hans waren verschillende belangrijke projecten simpelweg blijven liggen. En nu hebben we juist meters gemaakt!”
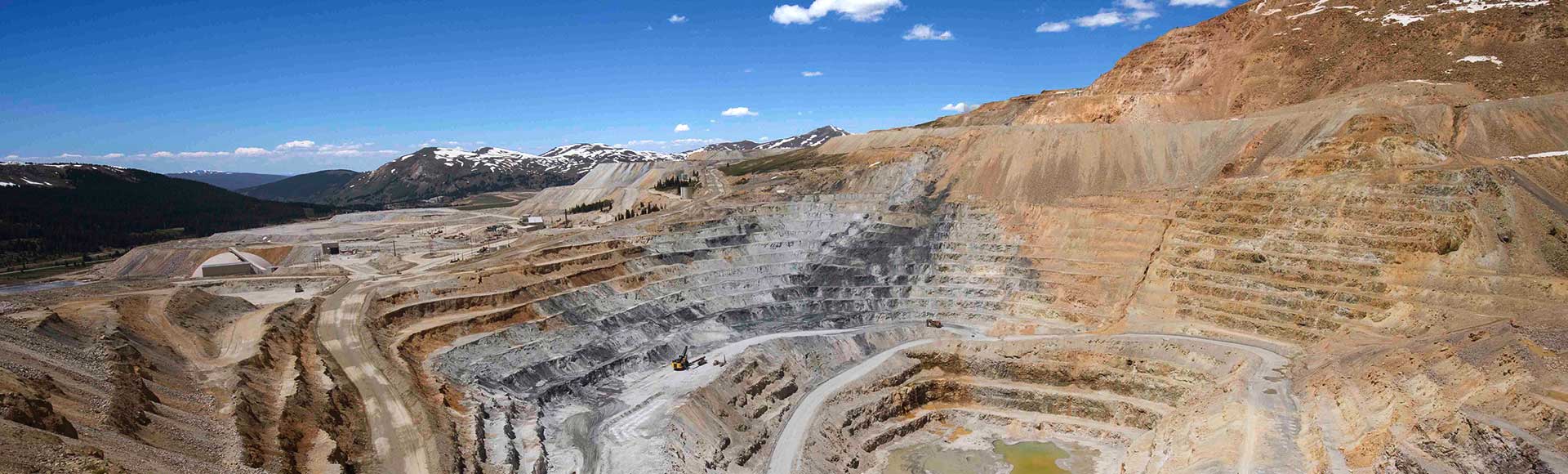
Op zoek naar inspiratie en verbetering?
Wil je meer informatie over de projectaanpak van Symbol? Neem dan contact met ons op via 053 – 20 30 240 of via onderstaand formulier. Wil je jezelf bekwamen in het optimaliseren van processen? Bekijk dan eens onze Lean Green Belt en Lean Black Belt trainingen!