Lean implementation at GGD Gelderland-Zuid: The spark became a fire!
In November 2014, the first employees at GGD Gelderland Zuid were trained in Lean. In the process, a number of pilots were launched to experience what Lean could mean in practice for the GGD. In a recent management review, the unanimous conclusion was that vetting the processes so far has paid off handsomely. In addition to reducing lead time and processing time, there is great enthusiasm among employees and management about practical work improvement. Meanwhile, more and more projects are being suggested from within the organization to be taken up!
GGD Gelderland-Zuid is the health service for 16 municipalities in the Nijmegen and Rivierenland regions and youth health care for 17 municipalities. The main task of the GGD is to monitor, protect and promote public health, with special attention to high-risk groups. It does this by preventing health risks and promoting the health of all residents. GGD Gelderland-Zuid was created on July 1, 2013 from a merger between GGD Regio Nijmegen and GGD Rivierenland. The GGD has about 400 employees. Its service area includes more than 536,000 residents.
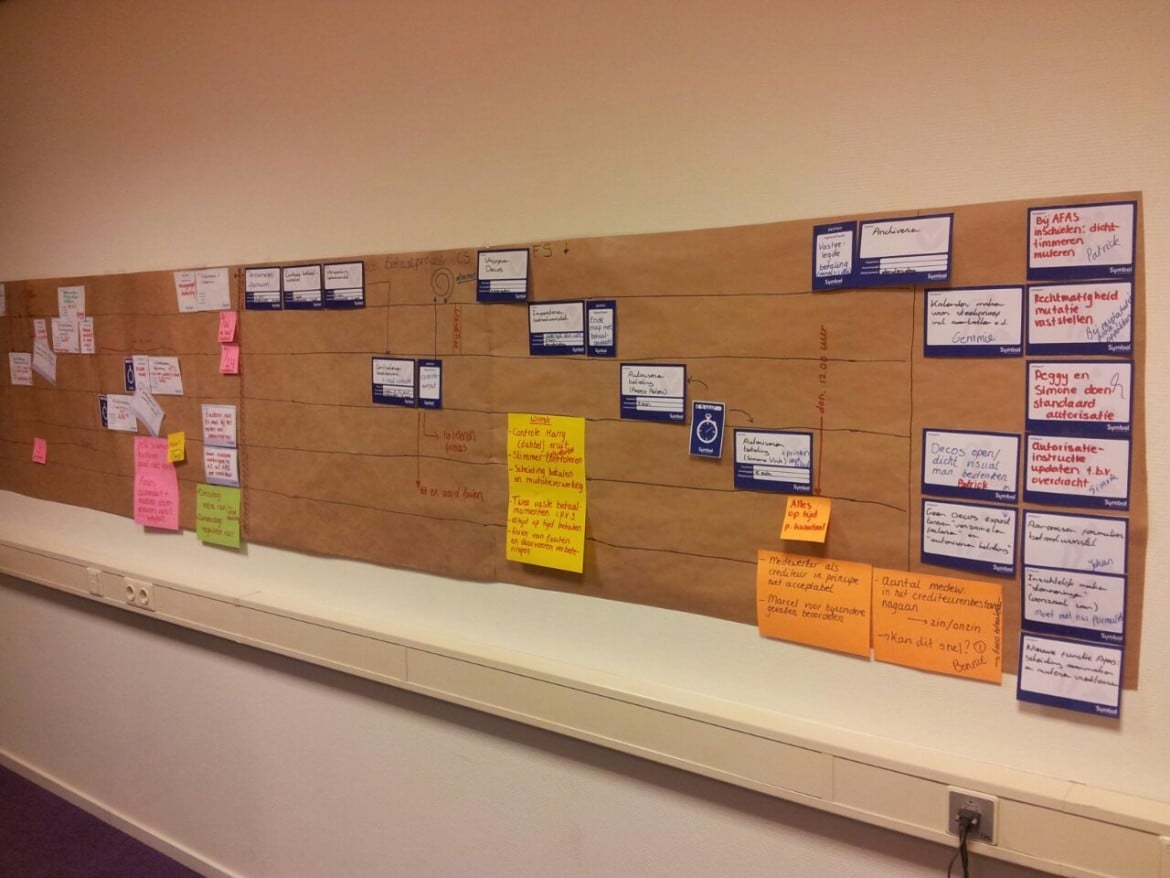
Value stream map at GGD Gelderland-Zuid: on the left the current situation and on the right the desired situation, including action points
“The spark became a fire.”
Ganny Boer is employed by GGD Gelderland-Zuid as Policy Advisor on Quality and Complaints Officer. The position is part of the executive office. With all the changes that have taken place over the past year, the organization is in a hectic period. “This dynamic is just really appealing,” Ganny said. “It is interesting to experience how crucial the function of the GGD is between citizens, care and service institutions and other parties such as housing associations, community centers, for example.”
The reason for introducing “Lean” into the organization was the fact that several colleagues had heard more about it and also wanted to bring this quality thinking into their own organization. Moniek Pieters has been director of GGD Gelderland-Zuid since September 2013. She has an affinity for improvement programs and is very open to initiatives from within the organization. That led to an introductory meeting in April 2014, a workshop-style meeting themed “Lean. “The spark quickly became a fire. The people in the organization became enthusiastic and wanted to proceed with a Lean process. Two consulting firms were then invited to present themselves and to come up with a proposal for the GGD Gelderland-Zuid. One of these agencies was Symbol BV. We clicked immediately with the Lean consultant from Symbol,” says Ganny.
Training of 14 employees and team leaders to become Lean Facilitators began in November 2014. This group included staff from the GGD, GHOR and Gelderland-Zuid Safety Region (VRGZ).
Pilots that produced immediate results
In conjunction with employee training, 5 pilot projects were launched within the organization to show what Lean could mean in practice for the GGD. These pilot projects focused on making some processes better and smarter and on creating a more effective workplace. “The organization was ready for this. What we do today can be better tomorrow was already an accepted fact.”
Ganny continues: “Mapping your processes also gave us a common focus, which in turn had a positive impact on the culture of the organization. One of the consequences of the projects is that we have the customer’s focus again. Earlier, for example, planning was done from the calendar, now from the customer. Also, some rooms are decorated differently. Superfluous items have been removed here.
Printers are set up in a logical location. The person on the phone scheduling appointments is now in a quiet place. You also realize more and more that you yourself are part of such a process. In front of me someone sits and I deliver something good at the right time for the person after me in the process. As a result, you see each other more as colleagues in the (connecting) process. Moreover, you become “refocused” on your tasks, so to speak. In other words, you get less and less inclined to want to rule over your tasks and work. This also gives air. Make sure your own tasks are finished within the process, of course while maintaining commitment. If everyone does that, the output will automatically be good.”
Eye openers
Recently, the progress of the Lean transformation was discussed in the MT of the GGD. This was also joined by the director of the Safety Region. The conclusion was unanimous that vetting the processes so far is yielding much for the GGD. In addition to reducing lead time and processing time (by eliminating duplication or introducing First Time Right, among other things), enthusiasm among employees and management about practically improving their work is high. Especially thinking from added value for the customer and thinking in integral processes instead of departmental processes is an eye opener for employees. More and more projects are now being put forward to be taken up.
“What struck me most in these trajectories? The willingness to improve was very high, the colleagues are ambitious. They have long realized that you can get things done together. Process-oriented thinking has been strengthened and of course the wastages have been made transparent, although not all of them are easy to solve. We have the customer more in mind. In the daily hectic that was sometimes forgotten.”
“We already have a natural desire to go for quality, and experience working pleasure in doing so. Working together to improve quality releases energy. You see that in all the pilots. It comes from thinking together, working together, self-reflection and awareness. Everything I do, I do in a process context. The feedback from the trainings has been tremendously positive. Something has been released that gives energy and joy. Last but not least, what is learned is also very applicable practically. In June, the MT will discuss how the Lean process will continue to be implemented. More people are expected to attend the Lean Basis and Lean Facilitator courses.
Do what suits your organization
“Tips for other organizations? Do what fits your organization’s culture. Introduce Lean from the demand of the organization. This suits us. Possibly in another organization (manufacturing company) a top down approach fits. Our choice is fine by me. The Symbol consultant was decisive in choosing Symbol. During the first meeting she explained in very practical terms what Lean means. She understood very quickly how we were in it, which gave us confidence. She also has extensive experience with Lean projects. We also find Symbol to be a very supportive organization. They immediately indicated that a subsidy was available for the project we wanted to implement. We also immediately found Symbol to be very well suited to our needs. This was reflected in the quotation and in the customized leaflet that was immediately printed, tailored to our organization.”
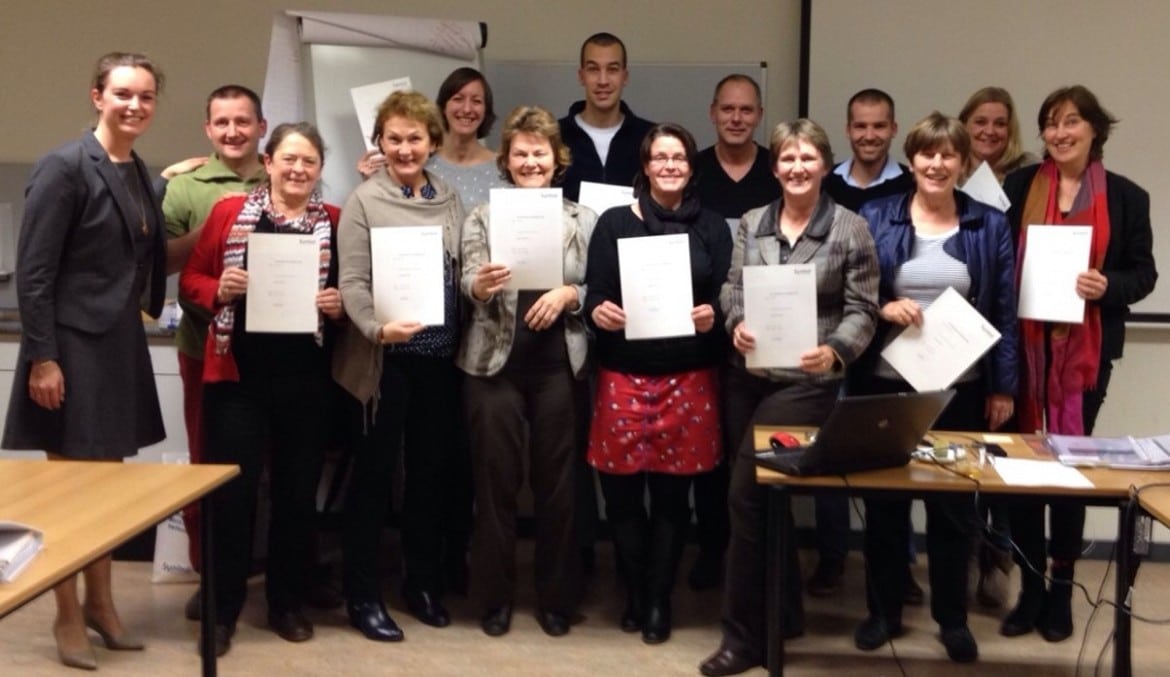
Lean Facilitators at GGD Gelderland-Zuid
Latest news/blogs
Klarna saved 40 million with AI but lost the trust of its customers
Klarna saved40million with AI but lost the trust of its customersThe question sounds absurd: how...
How do you eat an elephant?
Dutch productivity is falling again - and that offers precisely opportunitiesLabor productivity in...
From Theory to Practice: Junior Consultant at Stoneridge
From theory to practice: Junior Consultant at Stoneridge Before working at Symbol, Junior...