IATF:16949 at Shin-Etsu Silicones Europe
Shin-Etsu Silicones Europe – active in the Netherlands since 1949 – is part of Japan’s Shin-Etsu Chemical, a world market leader in PVC. Nicole, Marijn, Rens: already several consultants and junior consultants from Symbol have worked for this innovative company from Almere in recent years. “We really like working with Symbol. Symbol has a lot of knowledge, which we use gratefully in small and large projects,” says QA Manager Frank van der Wel. Recently it was the turn of junior consultant Ricardo Meulstee to join the global player.
IATF:16949 implementation
Frank: “At our production facility in Almere, Holland, we make sealing materials for the automotive industry. Some of our customers are Tier 1 suppliers: companies that supply directly to Original Equipment Manufacturers (OEMs) such as Toyota and Volkswagen, for example. Many of those OEMs require their suppliers to be IATF:16949 certified. That creates a chain reaction: preferably, as a Tier 2 supplier, we are also certified. So one of our customers asked us if we wanted to become IATF compliant. Although Shin-Etsu does not (yet) intend to be globally certified, we did not want to say “no” to that question, in order to keep the customer relationship optimal. But how do you tackle an IATF:16949 implementation if you don’t have the right knowledge for it? That’s why we enlisted the help of Symbol.”
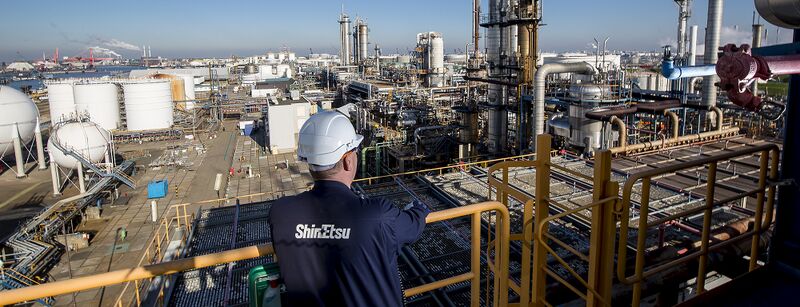
Work instructions in LeanForms
“I took over from Rens Tuller, who also started the IATF project here as a junior consultant,” says Ricardo. “It is up to me to further prepare the organization for the audit in 2024. This included describing processes and automating processes and workflows. Work instructions, for example, were still built in Excel, but because that tool is very error-prone, I suggested switching to
LeanForms. This is software from a partner of Symbol that allows you to build your own digital forms, including workflows. The first process we deployed LeanForms for was the customer complaints process.” That complaints process is now streamlined – exactly as the IATF standard requires of us,” Frank adds. “The process has been structured and professionalized, and we have a clear understanding of where our problems are. As a result, complaints are now handled faster. The long-term expectation is that this will actually reduce the number of complaints. And as for LeanForms, we are currently expanding it with other processes.”
Power BI implementation
In addition to LeanForms, Ricardo implemented Power BI, a tool from Microsoft, on his own initiative. “Even for KPI tracking, Shin-Etsu was still using Excel, but that doesn’t provide depth – Power BI does.” Frank adds again: “For the raw data streams we still use Excel, but with Power BI we now generate powerful (monthly) reports, including for the technical service process. The production department is also working with it. They are currently in the test phase and will go live with the tool in January 2024. After that, we will slowly expand to include other processes in our organization. The great thing about Power BI is that you use it to convert data into information. You no longer have to stare at large tables full of figures, but see a nice graph on a visually attractive dashboard. That makes it easier to steer on KPIs.”
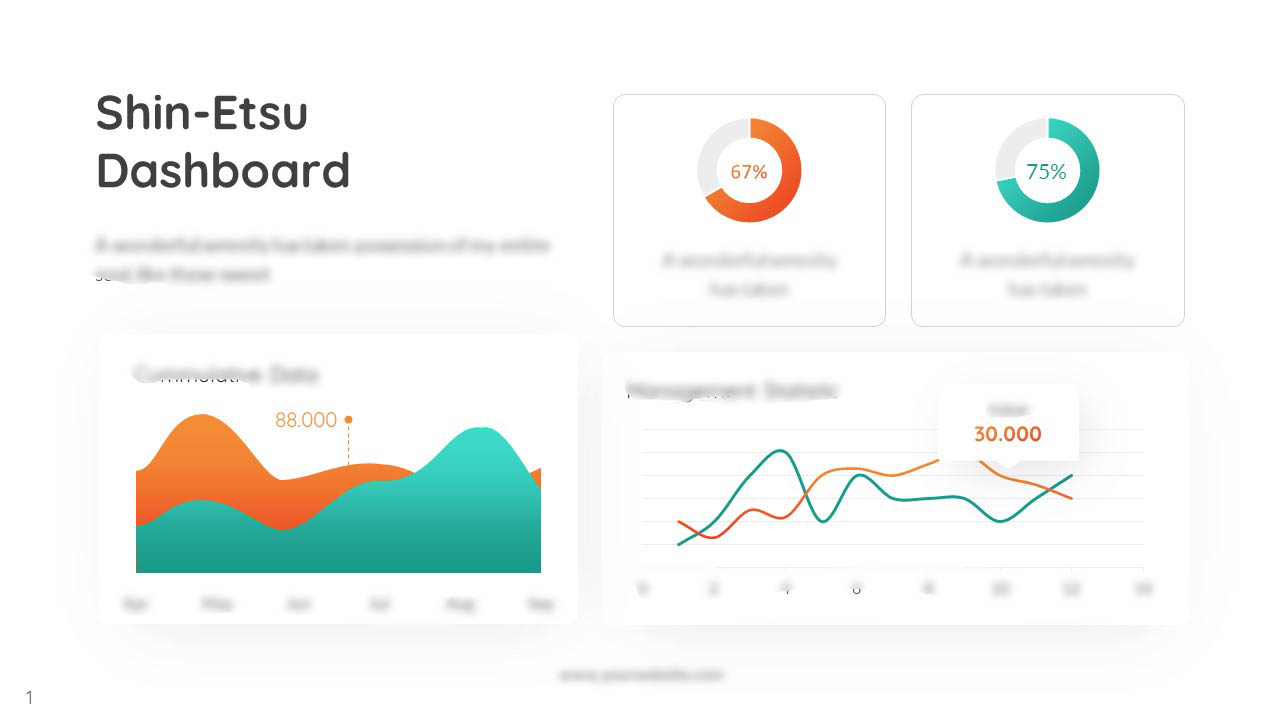
Rejection reduction
Another thing worth mentioning is the production data generation project that Ricardo initiated. “Right now there are still too many rejections, products they have to throw away, to comply with IATF. With data from the machines, Shin-Etsu will gain insight into exactly what happens during production – insight that is not there now. For example: if I press button A, how does this affect (the quality of) the product? Only when you collect and automate this data can you analyze it and then use it to make adjustments.”
Production process optimization
Frank: “What I like about Symbol’s junior consultants, such as Rens and Ricardo, is their hands-on mentality. They also have an open view of the work: ‘maybe something won’t turn out to be possible, but let’s try it first’. That has created enthusiasm in our team: we put our shoulders to the wheel together. And that’s also how the production data generation project came about, for example. We focused mainly on improving our test equipment – on the inspection side, in other words. Ricardo made us aware that it is now time for production process optimization. And that will help ensure that we can reach our goal next year. Becoming IATF:16949 certified.”
Looking for inspiration and improvement?
Want to learn more about Symbol’s project approach? Then contact us at 053 – 20 30 240 or using the form below. Do you want to train yourself in process optimization? Then check out our Lean Green Belt and Lean Black Belt training courses!