Continuous Improvement at ZGT: How 50 Departments Create Success Together
A safe-to-fail culture
Ramon Kamphuis – employed at ZGT for 25 years –
and Erwin van Dijk – employed at ZGT for 20 years – are jointly responsible for what is called “Attention to Improvement” within the hospital. “At ZGT, we want tomorrow to be better than today,” Erwin begins. “That’s why we are working on a safe-to-fail culture. This culture is essential to the success of Continuous Improvement at ZGT. As long as it is not at the expense of a patient or a colleague, you are allowed to learn, experiment and make ‘mistakes’. Because that’s what makes us better.”
Project weeks with motivated colleagues
That learning and experimentation happens, among other things, in the Lean Six Sigma project weeks that have been organized every spring and fall since 2006. Ramon explains: “Together with a group of colleagues from all layers of the organization, we spend four days on the field. In such a week we tackle three improvement projects and for each project the business manager is the client. If changes are desirable, they have to be mandated. We select the participants in the project week based on a stakeholder analysis.
We want to be sure that the colleagues who commit to the project are a good representation of the people who experience the problems we want to tackle in the improvement projects. And for the week to be successful, the prerequisite is that colleagues are intrinsically motivated.”
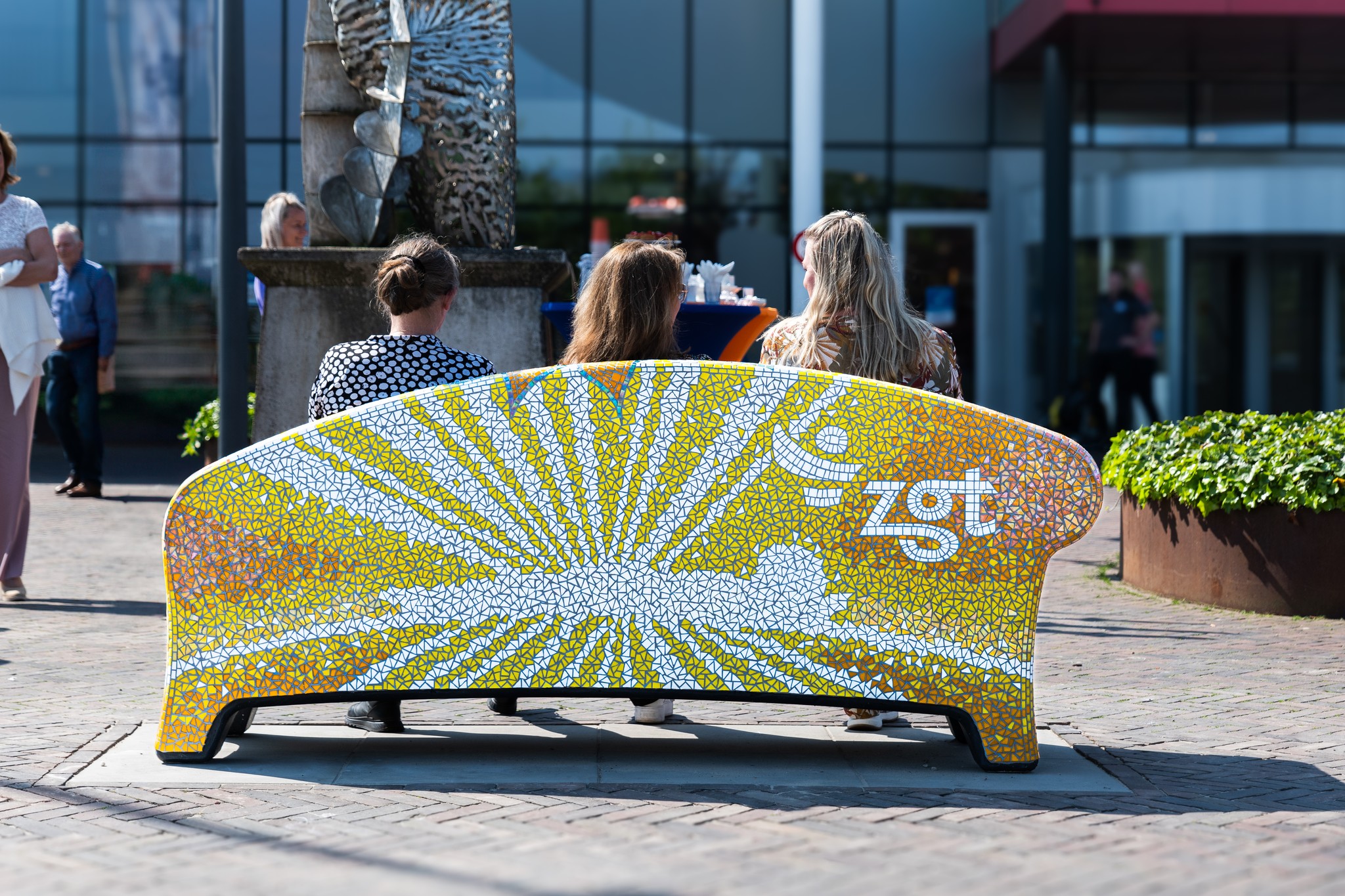
From project week to practice
“In the weeks before the project week, we map out the processes for each improvement project. We also collect relevant data. This involves data analysts in addition to participating colleagues. This thorough preparation ensures that we can assess all aspects of the problem we are tackling in an improvement project. After all, there is often more at play than people think beforehand,” says Erwin. “During the project week itself, the participants attend part of the Yellow Belt-level Lean Six Sigma training each morning. Then they work in teams on their own project, following the steps of the DMAIC model,” Ramon continues. “Of course, the teams are intensively guided by us during these days. In this we get help from our Black Belt colleagues Jeroen Egbers and Bram Drijfhout. On Friday afternoon, the teams present their project plans to the Board of Directors, and usually a delegation of the Cooperative Medical Specialists and members of the management team. In doing so, they ask for a go/no-go. In the event of a “go,” the team goes into practice for six months under our guidance to implement the project. During this period, review sessions are organized to discuss progress together. After these six months, we organize a return day in the same setting as during the final presentation. At this, the results are shared.”
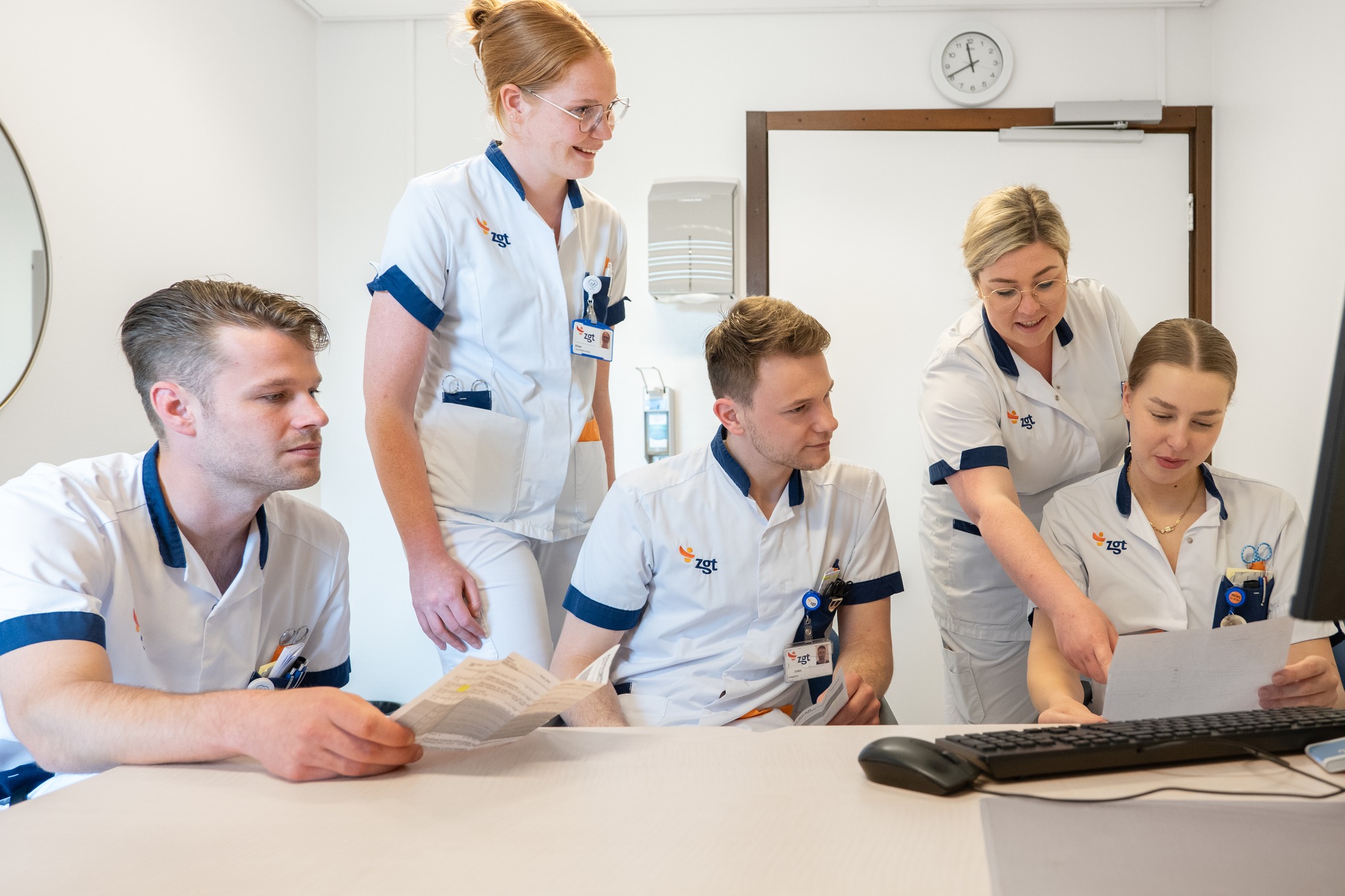
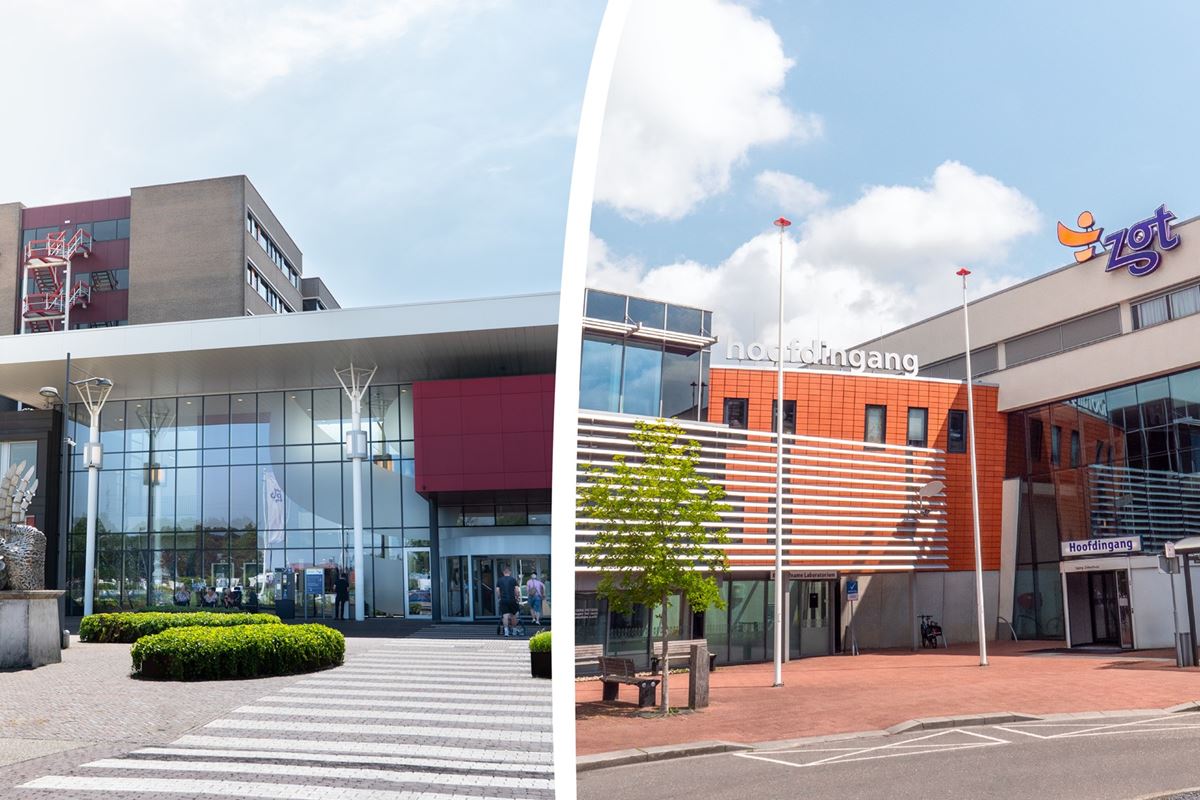
Pillars: short-cycle improvement and cyclical (de)regulation
The Lean Six Sigma project weeks are intensive and particularly suited to complex issues, such as collaboration in the regional transfer chain, the in, through and outflow of the ED process or the conversion of a regular treatment process to a fast track. “From the Board of Directors and the management team, we were asked a year and a half ago to develop a program outside of project weeks that would help create a culture of continuous improvement. For us this was also a logical step, because during the project weeks we were increasingly asked to help think about small processes that were not running smoothly,” says Erwin. “We had already developed concepts that could be used perfectly well for this purpose.” Ramon adds: “Moreover, the demand for care is rising while the number of care professionals is not increasing and the work pressure in care is already very high. So for sustainable employability, it is essential that we scrap everything that does not add value from the process and that we reduce internal regulations. That’s how we arrived at two pillars: short-cycle improvement and cyclical (de)regulation.” These pillars form the backbone of Continuous Improvement at ZGT.
Every department an improvement team
The plan: set up an improvement team in every department within ZGT to work with these pillars. The need for this is shown by the fact that teams enthusiastically signed up after receiving an explanation of the methods. Erwin: “As with the project weeks, we strongly believe that it really has to come from the employees. And fortunately there are plenty of motivated people. Of the 50 departments, we have now ‘had’ 22. After an intake with the unit head and some employees, in which we explain the concept and test whether there is intrinsic motivation, we set up the improvement team. In a training course on short-cycle improvement and cyclical deregulation, we provide the team members with the knowledge they need to work in a very structured way on problems that are not too complex. We translate the theory directly to the shop floor and vice versa. By picking up problems from the department and incorporating them into the trainings, it comes alive for people.”
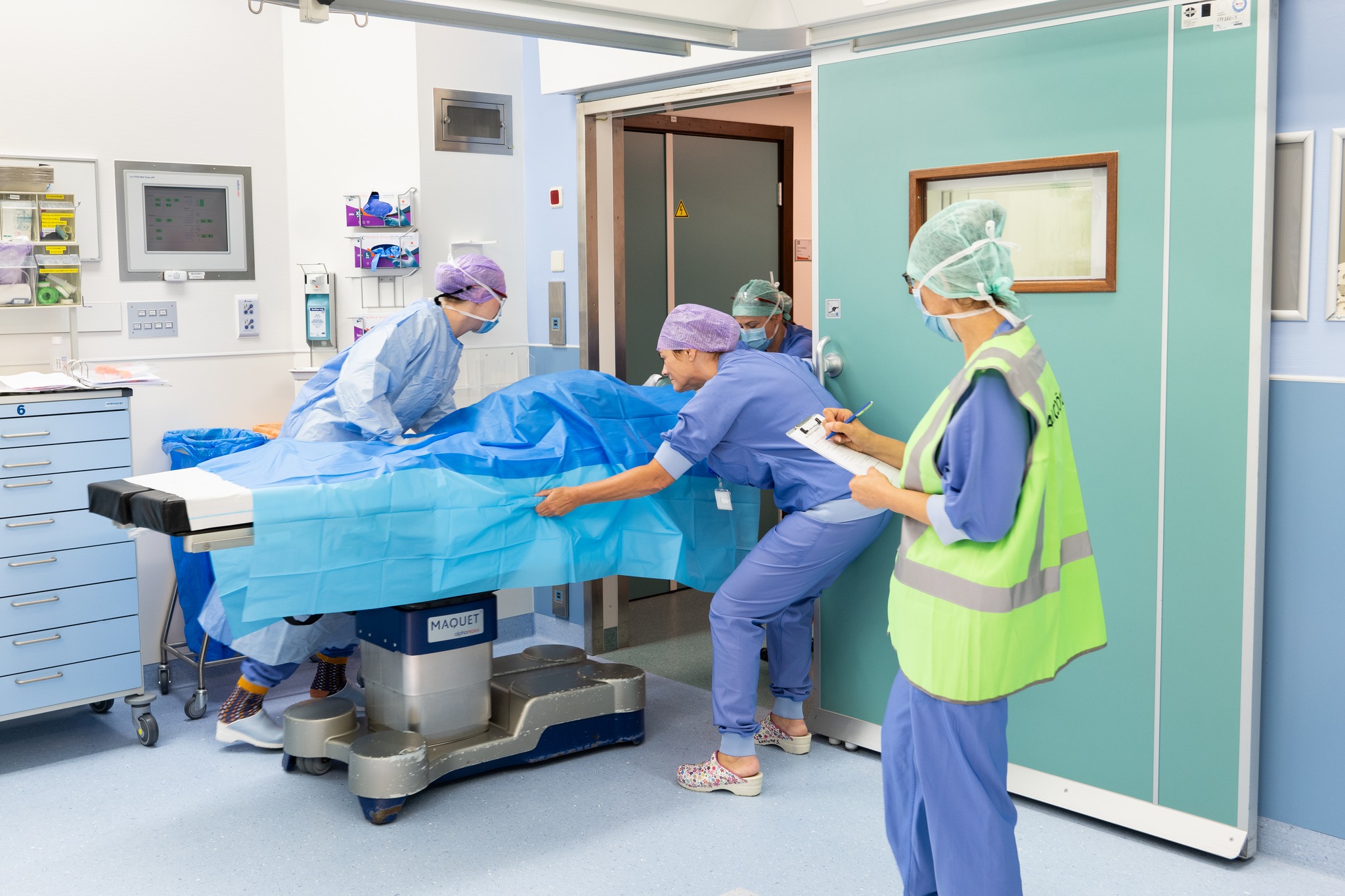
A snowball effect of improvements
Incidentally, it is not the case that such an improvement team then does everything on its own. “The people from the improvement team include other colleagues from the department in their process. So they really do it together,” says Ramon. “And the great thing is: the time freed up in one department can then be used for the next improvement project. This creates a snowball effect. An example: an outpatient department was constantly disturbed by incorrectly transferred calls. After going through the short-cycle improvement methodology, the cause became clear and a plan could be made with the parties involved to prevent this. This resulted in a significant decrease in these calls, saving the secretariats an hour a day of time.”
Lean Six Sigma Green Belt training by Symbol
The improvement teams are supported by Ramon and Erwin, as well as twelve Green Belts trained by Symbol. Erwin: “We wanted to organize the support better. So we looked closely at where our greatest needs lay. Not only at the level of improvement teams in the department, not only at the Black Belt level, but right in between. That’s how we came up with the idea of Lean Six Sigma Green Belt training. After all, what a Green Belt brings is, in our opinion, enough to make significant improvements in a department without it becoming too statistical. Through a call to unit heads, twelve colleagues from a variety of departments in the organization applied for the Lean Six Sigma Green Belt training. For this, we engaged Symbol.”
Training according to the CIMM methodology.
“I myself also got my Green Belt certification at Symbol, and I really liked both the class material and the instructor. So I was excited!”, says Ramon. “In addition, when making the choice, we asked colleagues in the organization who had already been trained. They too were enthusiastic about choosing Symbol.” Trainer Juan Jauregui adds: “Our trainings are organized according to the CIMM methodology, not losing sight of DMAIC. This means that our participants are trained in establishing an improvement system and improvement culture while at the same time picking up breakthrough projects. For this, they use DMAIC and other tools. Furthermore, our Six Sigma training courses are very comprehensive and high-level, and are delivered by professionals with extensive experience in data analysis.”
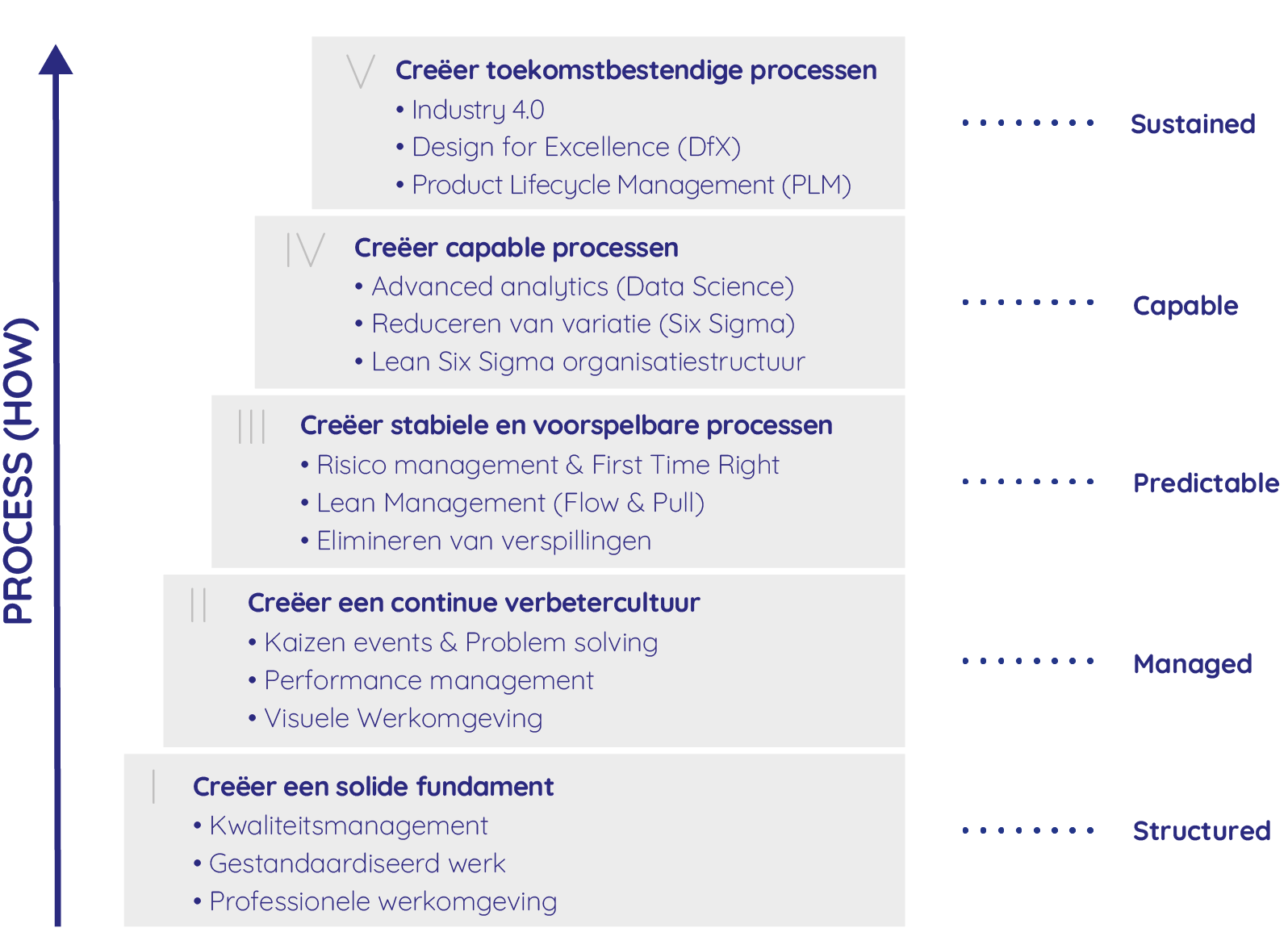
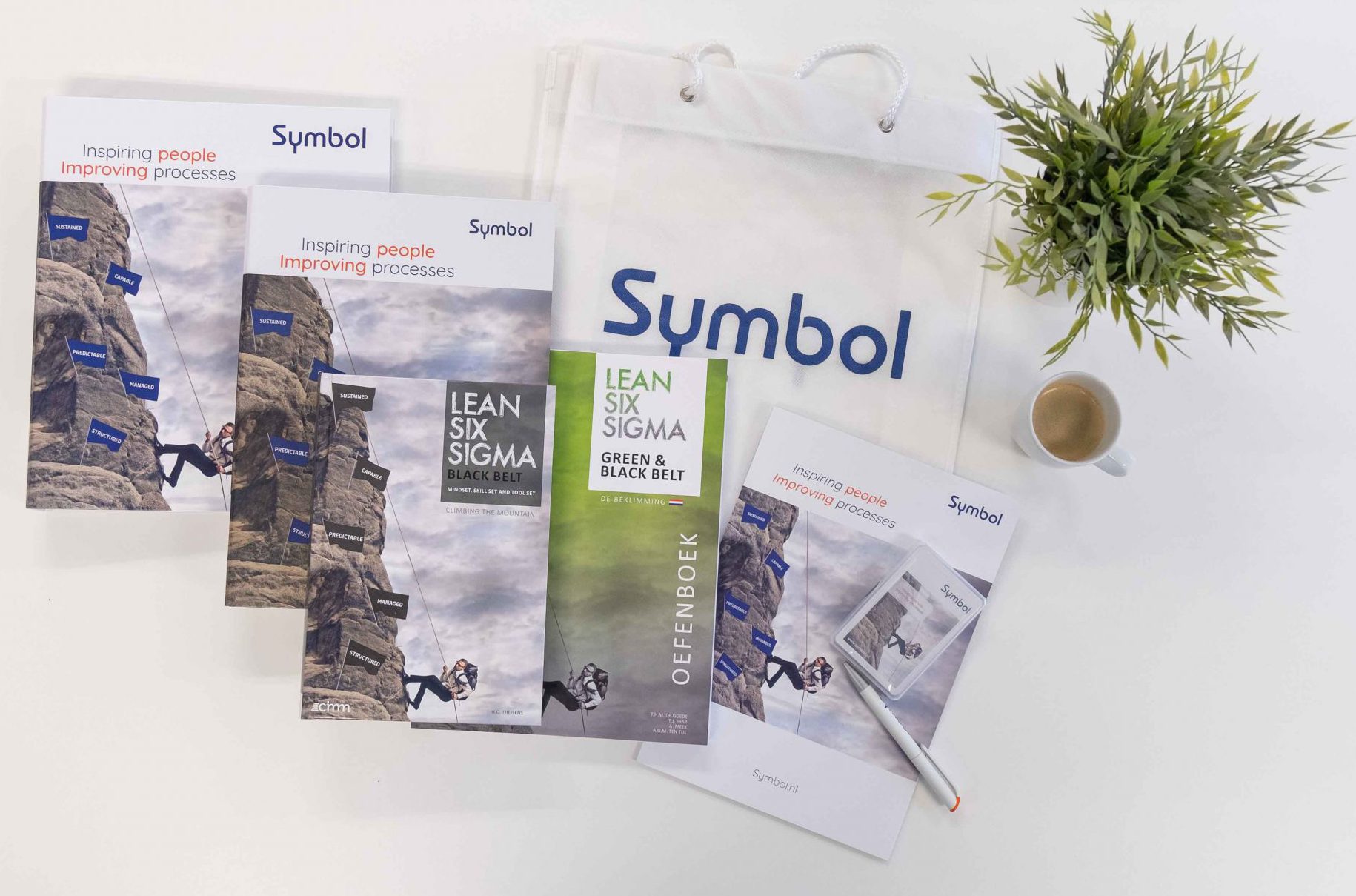
As many as 9 graduates
Ramon: “Not only that approach appealed to us, Symbol was also a pragmatic choice. They are in our region and had no problem giving the training in-company. And Symbol turned out to be a very good choice indeed, because the feedback from the participants about the training Juan gave was extremely positive. Eleven of the twelve took the exam and nine passed – with good grades. Normally the pass rate is around 45%. We think these results say something about both the participants’ drive and Juan’s ability.”
Like an oil slick through the organization
From Lean Six Sigma project weeks to establishing improvement teams and training Green Belts, ZGT is evolving. What is the next step? “The new Green Belts are currently deploying their knowledge only in their own departments. We want to explore how they can also share their expertise with other departments and thus be deployed across departments, enabling us to support the chain process. Possibly in the future we would like to have more Green Belts trained by Symbol,” says Ramon. “Finally, improvement teams have recently been building a digital portfolio,” adds Erwin. “Has an improvement been implemented? Then the team records in a system what went wrong in the process, how they solved it and what the result of that is. This is then shared with all the other improvement teams, so they can adopt the improvement if they want. This is how we create cross-departmental improvement teams – our ultimate goal. From the end of 2025, when all 50 departments within ZGT have their own improvement team, smart improvements will then spread through our organization like an oil slick.”
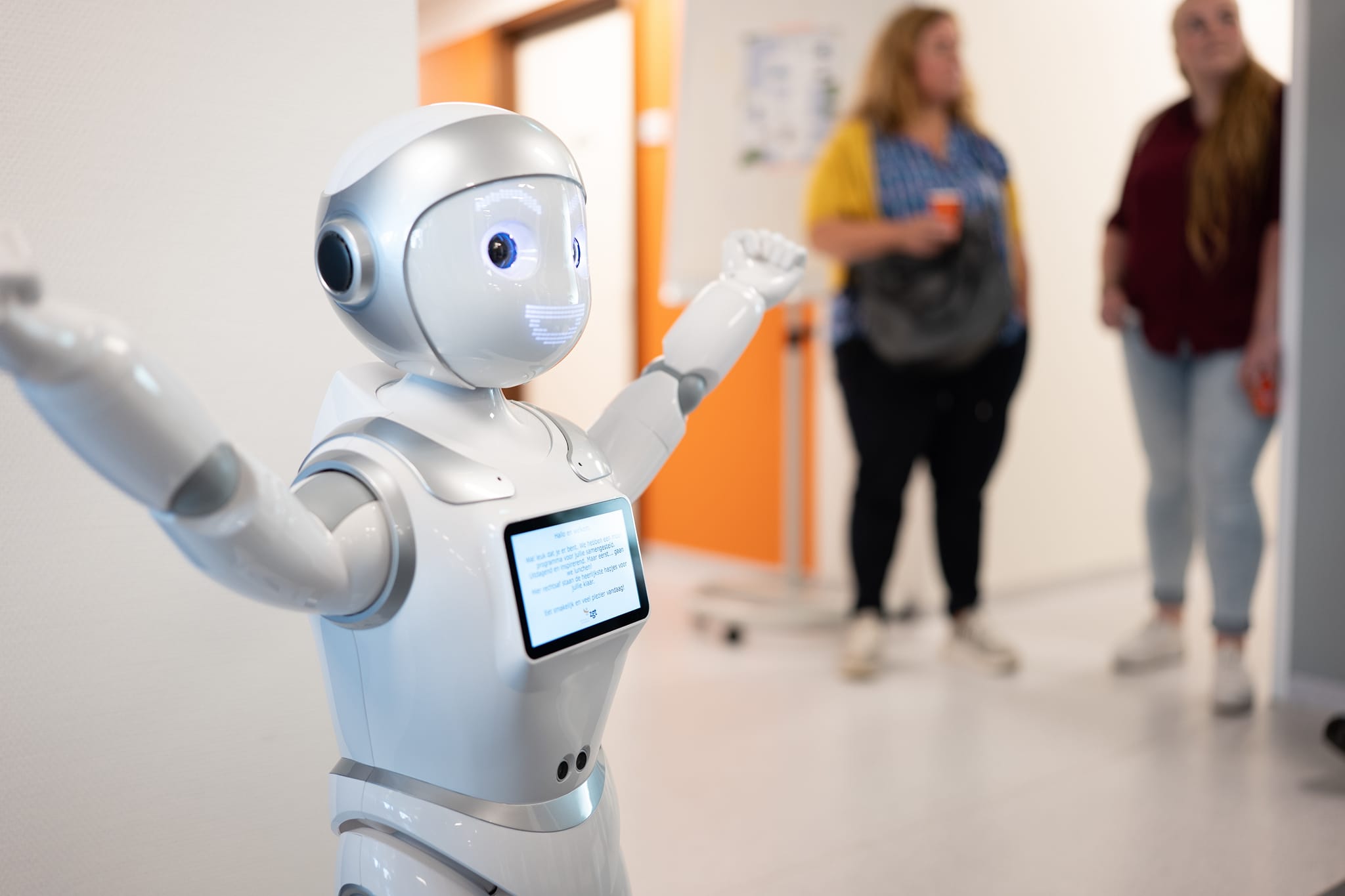
Looking for inspiration and improvement?
Want to learn more about Symbol’s project approach? Then contact us at 053 – 20 30 240 or using the form below. Do you want to train yourself in process optimization? Then check out our Lean Green Belt and Lean Black Belt training courses!