From ISO 9001 to IATF 16949
As consultants with expertise in ISO 9001 quality management systems, we are often asked how best to transition to IATF 16949. For suppliers, certification according to IATF 16949:2016 is an important prerequisite to participate in the automotive industry supply chain (OEM, tier 1, tier 2, tier 3). Small and medium-sized companies in particular often struggle with the complexity of automotive quality requirements. In particular, the development procedures, release, risk management and other regulations require a solid construction of the quality management system. Rapidly changing technological developments (e.g., electric driving, driver assistance systems, self-driving vehicles) require adaptive capacity of companies and their systems.
Quality Management
Often, quality management systems according to ISO 9001 have been implemented in the past without paying much attention to the effectiveness of the content. Development, production and inspection processes are often based on internal knowledge and experience. With increasing demands from the market, legislation and technological development, systems are becoming increasingly complex. In addition, quality management systems are maintained because the customer demands it.
Not infrequently, companies become active only a few months before the upcoming re-certification audit and bring the required documents and data back up to date. The requirements of IATF 16949 do not permit this mode of operation. As a result, companies will constantly have to design and apply their processes as the automotive industry requires.

The transition from ISO 9001 to IATF 16949 is seen by Symbol in four main phases
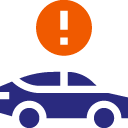
1. The gap analysis
This stage is designed to accurately identify the status of the quality management system. This is based on the existing processes, procedures and practices, which are tested against the IATF 16949 standard. This helps to understand where the company still has shortcomings to meet the standard requirements.
The main outputs are a gap analysis and a plan of action.
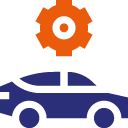
2. The transition
In this phase, the existing quality management system is converted/improved to the standard requirements to be added. Not infrequently, a company decides to rebuild and digitize its quality management system. Integrated management systems in particular cannot function without a solid document structure. In addition, implementing process descriptions, recording quality data and good form structure is very important. This keeps the management system workable and accessible. Our experiences in the automotive sector have given us valuable insights that we are happy to share.
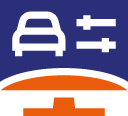
3. Implementation and certification.
In this phase, the new management system will be put into operation. After the process descriptions and registrations are implemented, the company has about 6 months to prepare for certification by an accredited certification agency. As a provider of IATF 16949 training and implementation consulting, our experts are ready to support companies in successfully achieving this certification.
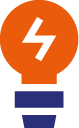
4. Additional trainings
During this period, additional training such as IATF & Core Tools and IATF 16949 Internal Auditor is often provided to key process owners.
Continuous improvement in the automotive sector
After the new quality management system is certified, the company will meet the requirements to be able and allowed to supply in the automotive industry supply chain. It remains important at all times to adapt the management system to constantly changing requirements. Companies working with Lean or Lean Six Sigma are accustomed to continuously improving their processes.
By closely following the publications of AIAG, VDA QMC and other umbrella organizations, changes to standards and requirements do not come as a surprise.
Discover how transitioning from ISO 9001 to IATF 16949 can accelerate growth and innovation. Take the leap today with our expert guidance and proven approach. Start now by contacting us.
Also interesting to read
From Theory to Practice: Junior Consultant at Stoneridge
From theory to practice: Junior Consultant at Stoneridge Before working at Symbol, Junior Consultant Wisse Bos had never heard of a Production Part Approval Process (PPAP). Now he knows all the terms associated with a PPAP - such as PSW and PCN - like the back of his...
Optimize Quality Management with AI Tools
Optimize quality management with AI tools In the modern business environment, quality management is becoming increasingly important. Companies strive to provide high-quality products and services to ensure customer satisfaction and market competitiveness. Quality...
The Netherlands’ youngest Black Belt speaks
A ideal is not yet not a solutionEmiel recently gave a training session on the topic of problem definition and measurable requirements.During the session, he gave several times the feedback that it is not necessary, and may even be undesirable, to think about...