Workplace organization through the Lean 5S method
Boxes are stacked up in a corner, packing materials lie next to them. Post-its and work orders form a large, untidy pile on various desks. In the workshop, tools are mixed up. Such a chaotic work environment – does more harm than you might think. The solution to this is 5S workplace organization, especially for organizations in industries such as manufacturing, Food & Pharma and healthcare.
Learn more about 5S in the workplace
A step back. After all, why would you want to know more about 5S workplace organization? The first reason is simple: an uncluttered workplace or work environment causes employee productivity to decline. The main reason is waste. Documents on the computer, tools or inventory: you can probably imagine how much time is wasted because employees lose things when they need them. And apart from the time lost, losing things can also create dangerous situations. Especially in the case of sharp objects or tools. Eliminating waste is at the heart of Lean Management. Initially these applied to manufacturing processes (think 5S Toyota) but today they apply to any kind of process. With 5S, you can also act more efficiently on the shop floor or in the office by paying attention to waste. A chaotic workplace also produces stress and distractions. In a clear environment, it is a lot easier to think clearly and sharply.
Philosophy behind the 5S method
Also, a disorganized workplace has a negative effect on relationships with your customers. The philosophy behind the 5S method is that if your organization doesn’t get the simple things right, you won’t be able to make high-quality products, or execute complex projects, either. If the work environment is well organized, it reflects positively on the attention your organization pays to customers, products and employees. Not for nothing is it even common in the automotive industry for customers to conduct a 5S audit of their suppliers.
The five steps from the 5S program
So 5S is about smartly organizing your work environment and operations. Safe, efficient and professional. It is the basis for creating a culture of continuous improvement. The 5S program consists of five steps:
- Separate: no unnecessary things in the workplace;
- Arranging: everything has a fixed place;
- Cleaning: constantly ensuring a neat and orderly workplace;
- Standardize: make visual agreements, establish procedures and regulations;
- Upholding: securing standards and discipline.
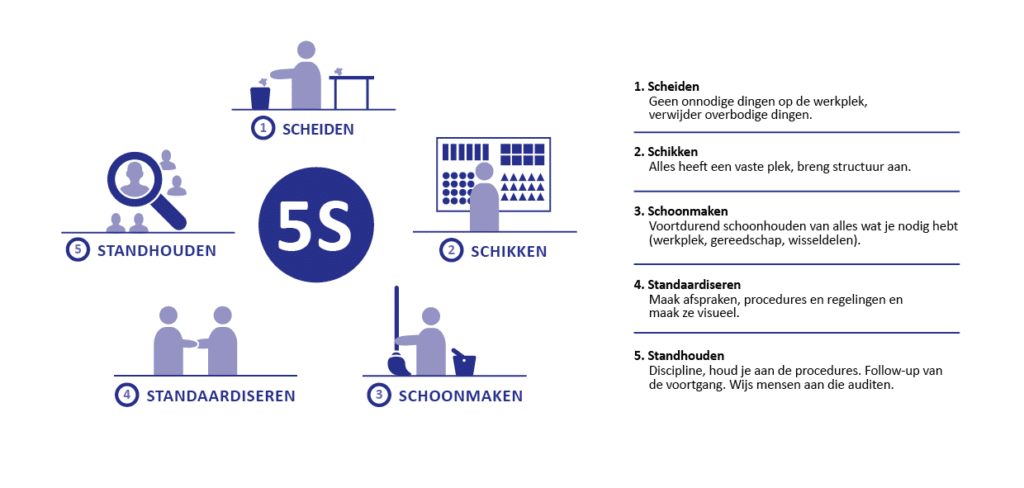
S1: separating
This step distinguishes between the necessary and unnecessary items in the workplace. The unnecessary items are removed.
S2: arranging
This step involves deciding on the right place for the necessary items. Based on frequency of use, how much of all necessary items is determined and where it is stored. To give an example, tools for machinery are hung on a shadow board, using markings, labels, and color coding so that you meet the safety standards of NEN 3011.
S3: cleaning
Cleaning is a form of inspection. In this step, therefore, you remove clutter, dust, dirt and debris and ensure that tools, equipment and the workplace are clean and maintained. Not once, of course, but on an ongoing basis. You may think that the “cleaning” step is unnecessary for your organization because you outsource the cleaning of the workplace and machinery. But cleaning is more than just wiping a cloth over something. What matters is active employee ownership of his or her workplace or machines. As a result, defects are identified early and causes of contamination are eliminated. Consider, for example, a pneumatic hose that is full of dust, making it impossible to see that the hose is porous and in need of replacement.
S4: standardizing
Standardizing means agreeing on how everyone in your organization works. Without this step, all other steps are redundant. Unfortunately, standards often do not work because they are too complex, too long or outdated, or because they are not enforced or tested anyway. Within 5S, making standards, procedures and regulations visual is the norm so that all agreements are clear at a glance.
S5: stand your ground
Step five is to stand firm. You do this first of all by working according to the standards (see above), but also by evaluating regularly through 5S audits. The ultimate goal is for everyone – from shop floor to management team – to participate once in a 5S audit team. This in fact creates a good cross-pollination, as each audit team has its own insights. Then sharing the results with the entire organization keeps everyone focused and on track.
The results of 5S
Of course, these five steps in 5S produce the necessary results, such as:
- Lines have been drawn on the floors of production and warehouses and there is
indicated what should be where; - Cords are neatly tucked away everywhere;
- All safety aspects are well completed;
- Tools hang on shadow boards;
- Workstations are conveniently arranged;
- There is no more stock than strictly necessary;
- Standard operating procedures are understandable to all.
5S coordinators in your organization
Like hiring a Lean Facilitator, appointing multiple 5S coordinators (the project team) also contributes to the successful implementation of the 5S method. These employees are given different tasks. For example, they are the point of contact for 5S actions and initiate and guide improvement proposals. In addition, they help create an audit plan (which the audit teams can use as a basis), oversee implementation and report to the management team. In short, appointing a project team of 5S coordinators monitors the progress of the 5S process and maintains the knowledge of 5S within your organization. Of course, the 5S coordinators are trained, coached and mentored by Symbols Lean Facilitator throughout the project.
Evaluate 5S
After the pilot, it makes sense to evaluate 5S with all employees involved as well as the management team. Does the workplace now meet the standards? Are the audits being done properly and what is coming out of them? Is 5S part of daily activities? Once the 5S process of maintaining and improving is embedded and the proper discipline is in place, the responsibility for maintaining 5S can be transferred to a single appointed manager in your organization. The Lean Facilitor has done his or her job and you can disband the project team – but above all, don’t forget to celebrate the success together.
5S in practice
Symbol has already guided many clients in implementing 5S. For example, read the story behind the 5S implementation at Flos.
Starting with 5S
After reading the above results, are you convinced of the importance of the methodology and want to implement the 5S method? Then our recommendation is to begin by mapping out your current situation and describing your intended situation. You will do this together with the management team and all employees involved. All employees indeed, because 5S is a reflection of the entire organization. Depending on your current situation, you can then start a pilot, with the responsibility for implementation lying, of course, with the employees.
However, for success, it is essential that they are coached and guided in this process by an experienced 5S Lean Facilitator. You can find those at Symbol. At the beginning of the process, an experienced Symbol consultant conducts 5S training at your location. After that, several hands-on 5S sessions will be organized, going through the five steps of 5S. Your Lean Facilitator can also help you with the first step: mapping your current situation and describing the intended situation.
In short, start right away with increasing productivity in your organization using the 5S method. Symbol helps you do just that!
Register for one of our training courses, for example Lean Green Belt, Lean Black Belt, Lean Six Sigma Green Belt, Lean Six Sigma Black Belt and learn all about improvement methodologies. 5S is part of this.