Operational Excellence
What is Operational Excellence
The Operational Excellence strategy focuses on an optimal delivery process based on customer expectations, without errors, on time and in a cost-effective manner. Symbol helps companies implement this strategy effectively.
To better determine in which direction an organization should develop, Treacy and Wiersema’s value strategy model is often followed. Three generic value strategies help organizations develop an appropriate strategic and operational plan, namely: Operational Excellence, Customer Intimacy (Customer Partnership) and Product Leadership (Product Leadership). According to Treacy and Wiersema, a company must excel in one of these three value strategies while performing at an acceptable level in the other two strategies.
Symbol specializes in Operational Excellence, looking closely for consistency with the other two value strategies.
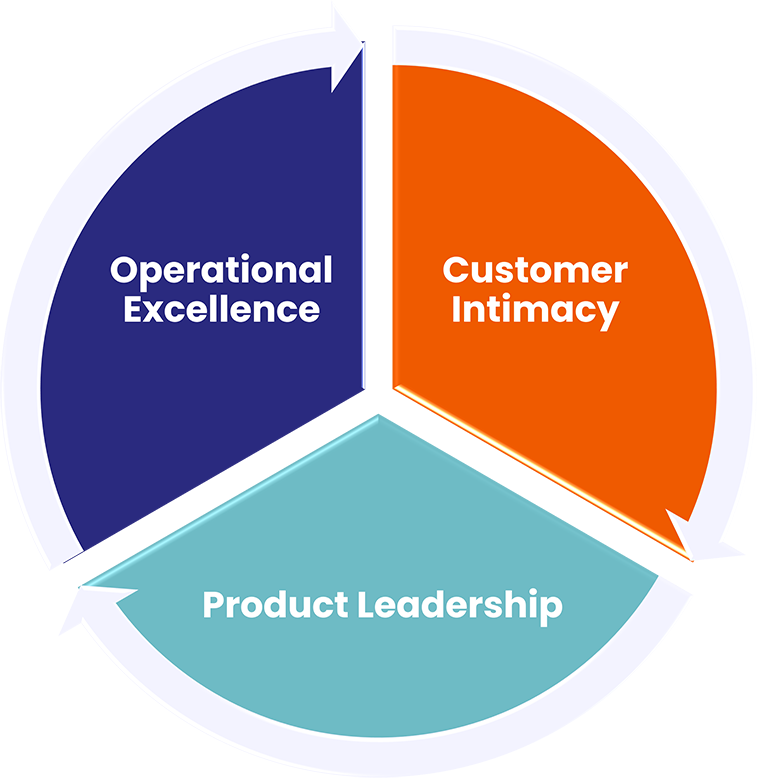
Principles of Operational Excellence
Guidelines for Operational Excellence
Problem solving and training
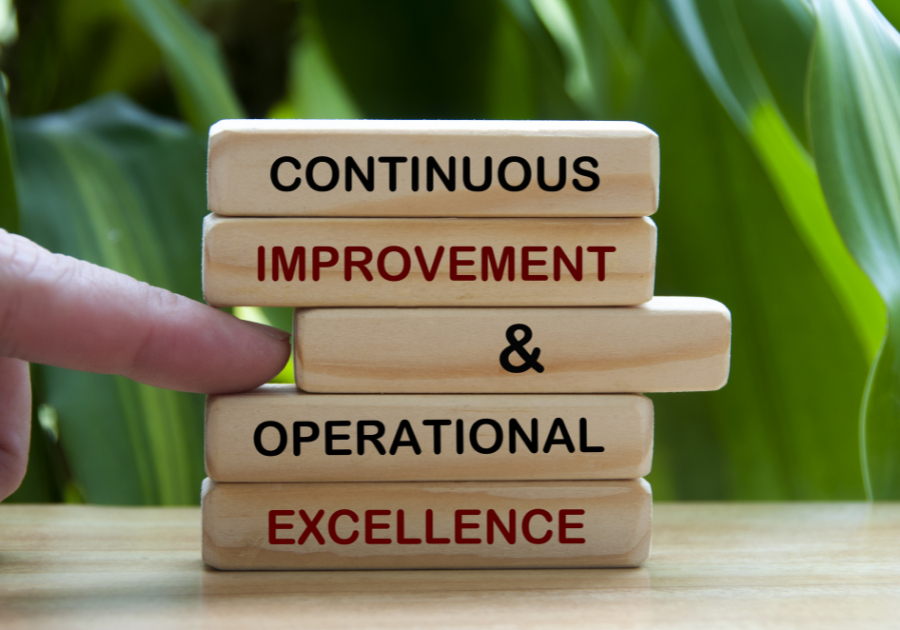
200,000 euros savings per year at Tata Steel
Tata Steel has achieved Operational Excellence with Six Sigma data analytics, in partnership with Symbol. This approach has resulted in substantial savings and efficiencies, such as saving more than €200,000 annually on iron transportation and speeding up the steel coil feeding process.
Results:
✅ Cost savings of over 200k on iron transportation.
✅ Savings of tens of thousands of dollars through faster steel coil entry.
✅ Development of Data Lake in cloud.
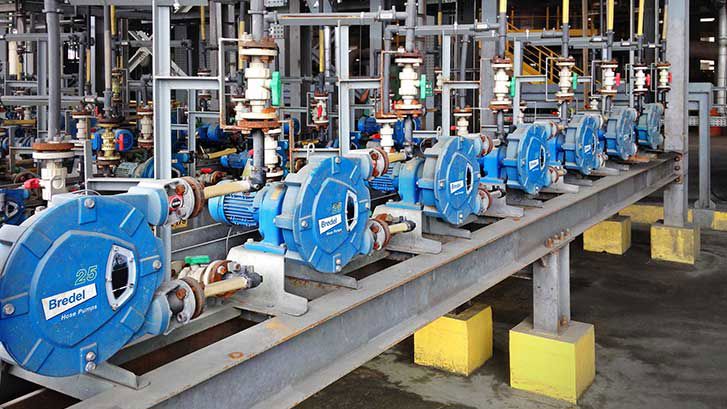
Increased safety and efficiency at Watson-Marlow
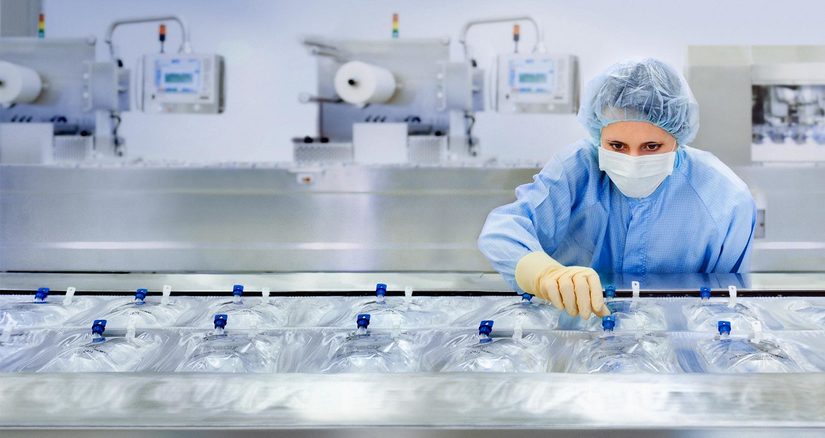
90% OEE at Fresenius Hemocare
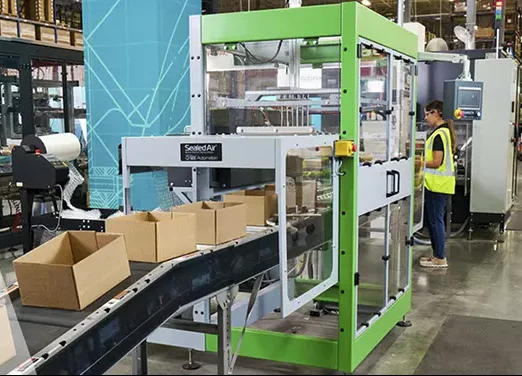
Process improvement at Sealed Air
people certified in Lean Six Sigma
elevated organizations to a higher level
years of lasting impact
Increase efficiency and quality
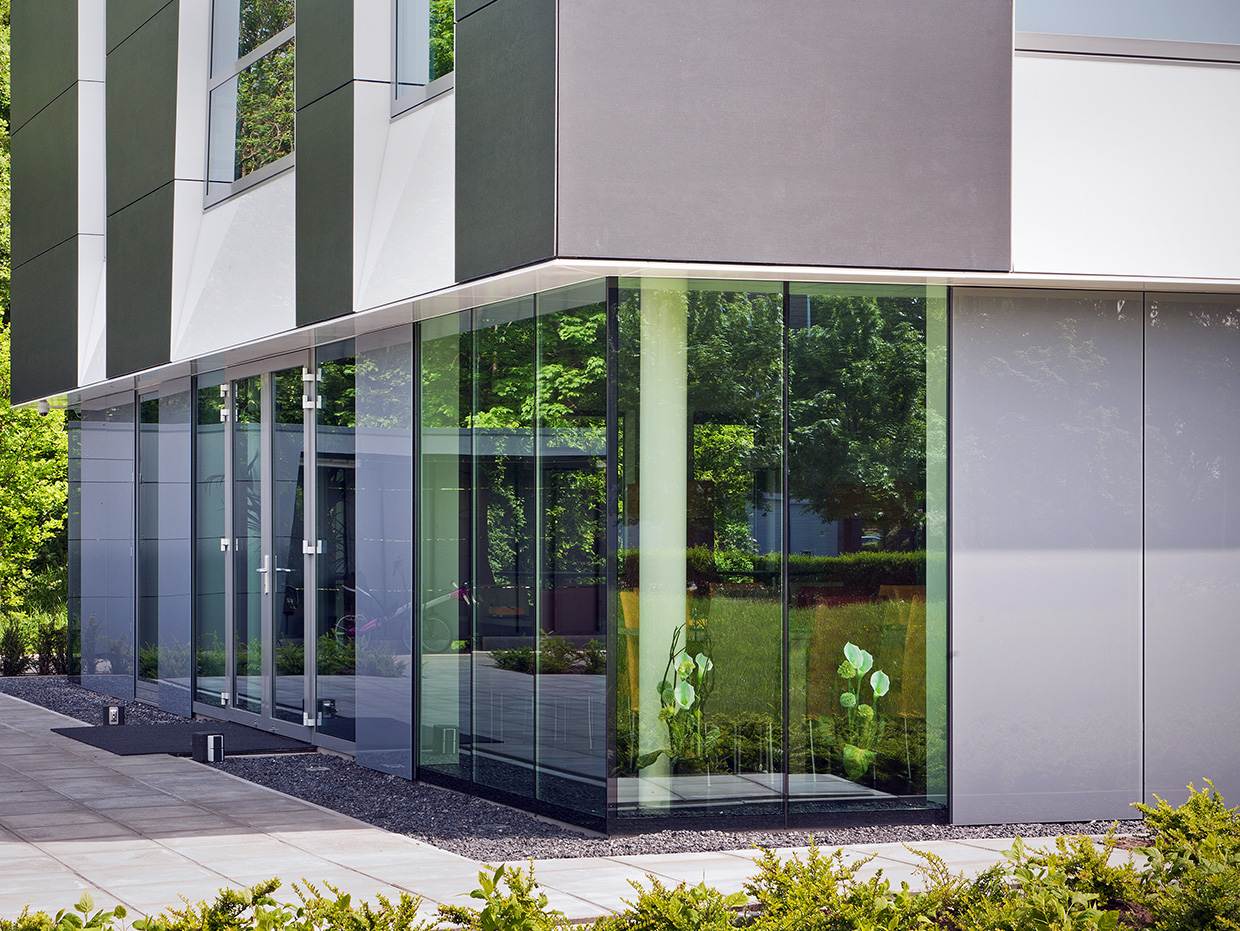
Join forces with us
Do you have questions or want to learn more about how we can support your organization in achieving Operational Excellence? Then please fill in the contact form. One of our experts will contact you shortly. We look forward to hearing your questions and discussing how we can work together to achieve sustainable improvements in your organization.