Lean Management
Is operational performance lagging behind targets? Are there dissatisfied customers or problems with quality? Are lead times too long and inventories too high? Are operational costs rising? Are employees getting stuck in the daily process of continuous improvement and problem solving?
A Lean transformation offers a solution. Depending on the current maturity level and issues, Symbol helps organizations shape a transformation and implement it successfully.
Sustainably better results through structured approach and proven Lean techniques
We have helped many companies and organizations with our Lean transformation approach. In doing so, we look at three elements of the puzzle: Strategy, Realization and Competency Development. First, it determines the current maturity level and the breakthrough projects needed to flesh out the strategy. Implementation of the right building blocks and realization of improvement projects are at the center of realization. The Competency Development puzzle piece focuses on engaging, training and coaching employees.
Our approach demonstrably results in shorter lead times (up to 75% shorter lead time), better quality (up to 100% first time right) satisfied customers and significantly lower operating costs.
Strategy
From the vision of the organization, together with management and MT (Management Team), a strategy for continuous improvement is established. In Lean terms, we call this the “True North. As input, we use the CIMM assessment, a number of interviews and the Gemba observation. We design a transition program consisting of a number of breakthrough projects (management priorities) and a number of CIMM building blocks. These are turned into improvement projects that contribute to achieving the goals.
Competency Development
How do you engage, enthuse and support, your employees in achieving lean transformation goals? Together we design a development plan for directors, managers and employees. By attending training, knowledge and skills are gained. We then coach people while implementing improvement projects. We coach management in their role as Champion.
Realization
From the strategic or operational objectives, projects are selected and teams are assembled and responsibilities are laid down. Project leaders are assigned to the improvement projects and employees become team members. We coach teams in the implementation of the lean transformation, but also provide junior consultants and interim managers who can take on projects if required.
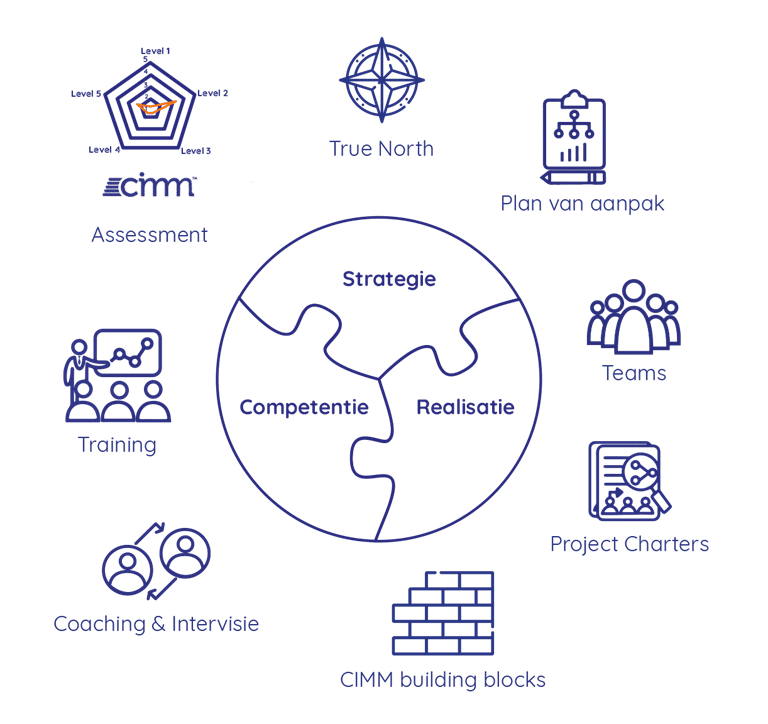
Roadmap for successful Lean Management
Symbol’s Lean transformation model provides a structured approach, embedding new ways of working within the organization. This plan has nine elements:
Understand the current situation
Map the current maturity level of the organization
CIMM™ Assessment
.
Create vision (True North)
Define clear goals for the Lean transformation and communicate them to all stakeholders.
Create engagement from the core team
A core team ensures support in the organization. Clear communication is key to getting all employees excited about the transformation.
Identify opportunities for improvement
Map out where opportunities for improvement exist. Analyze processes and identify waste. Prioritize improvement opportunities based on impact and feasibility.
Implementation of the improvement strategy
Select appropriate techniques (CIMM-building blocks) and breakthrough projects. Appoint a project leader (facilitator) and assemble the team.
Create a culture of Continuous Improvement
Get the organization appropriately involved and actively contributing. Organizational Behavior Management (OBM) helps develop proper attitudes and behaviors.
Monitor and measure progress
Use performance indicators (KPIs) to measure performance and identify deviations from it. Steer the right way.
Embedding in processes
Improvements must be secured in the organization for lasting results. Work instructions, Poka Yoke, training and audits contribute to this.
Keep learning and improving
Continue to learn from successes and failures and invest in developing employees competencies through training. Encourage experimentation and learning.
Faster Vaccinations at GGD Thanks to Lean
Symbol helped GGD GHOR increase vaccination rates during the corona pandemic by applying Lean methodologies to puncture sites in the Netherlands. This led to significant improvements in efficiency and throughput, resulting in 1.4 million punctures per week at its peak.
Results:
✅ Vaccination rate increased from 22 to 50 shots per hour.
✅ Implementation of Lean techniques at 50 vaccination sites.
✅ Improved work balance and flow of visitors.
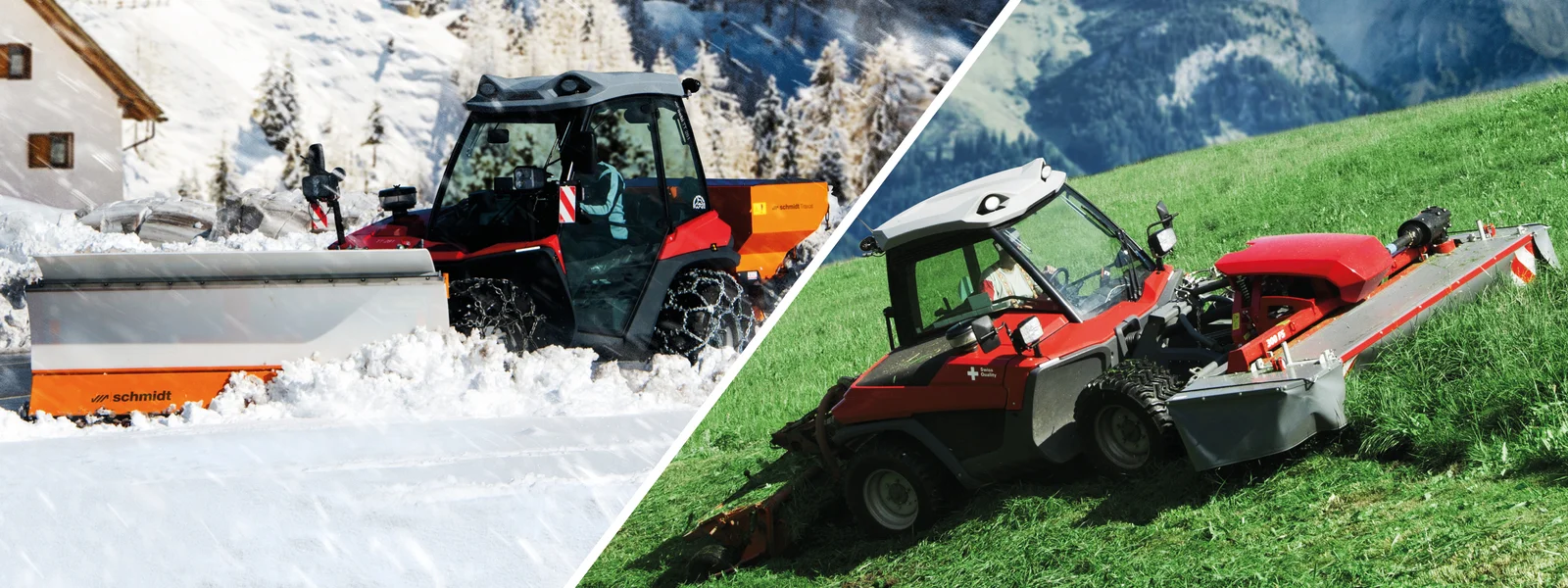
Lean improvements at Aebi Schmidt
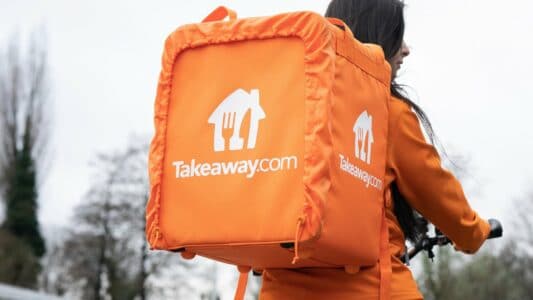
Lean success at Scoober/Just Eat Takeaway
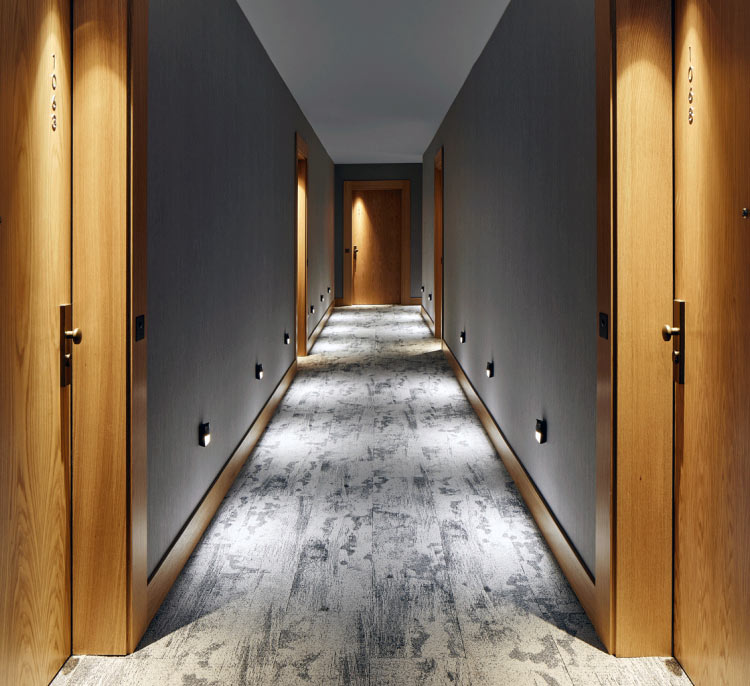
Reinaerdt Doors cuts delivery time by 56%
people certified in Lean Six Sigma
elevated organizations to a higher level
years of lasting impact
Improve your organization with Lean Management
Achieve lasting improvements through the use of structured approaches and proven techniques. Through the Lean transformation approach, your organization will learn to make large and small improvements independently. As a result, your organization will achieve its financial and operational goals. This leads to satisfied customers and employees.
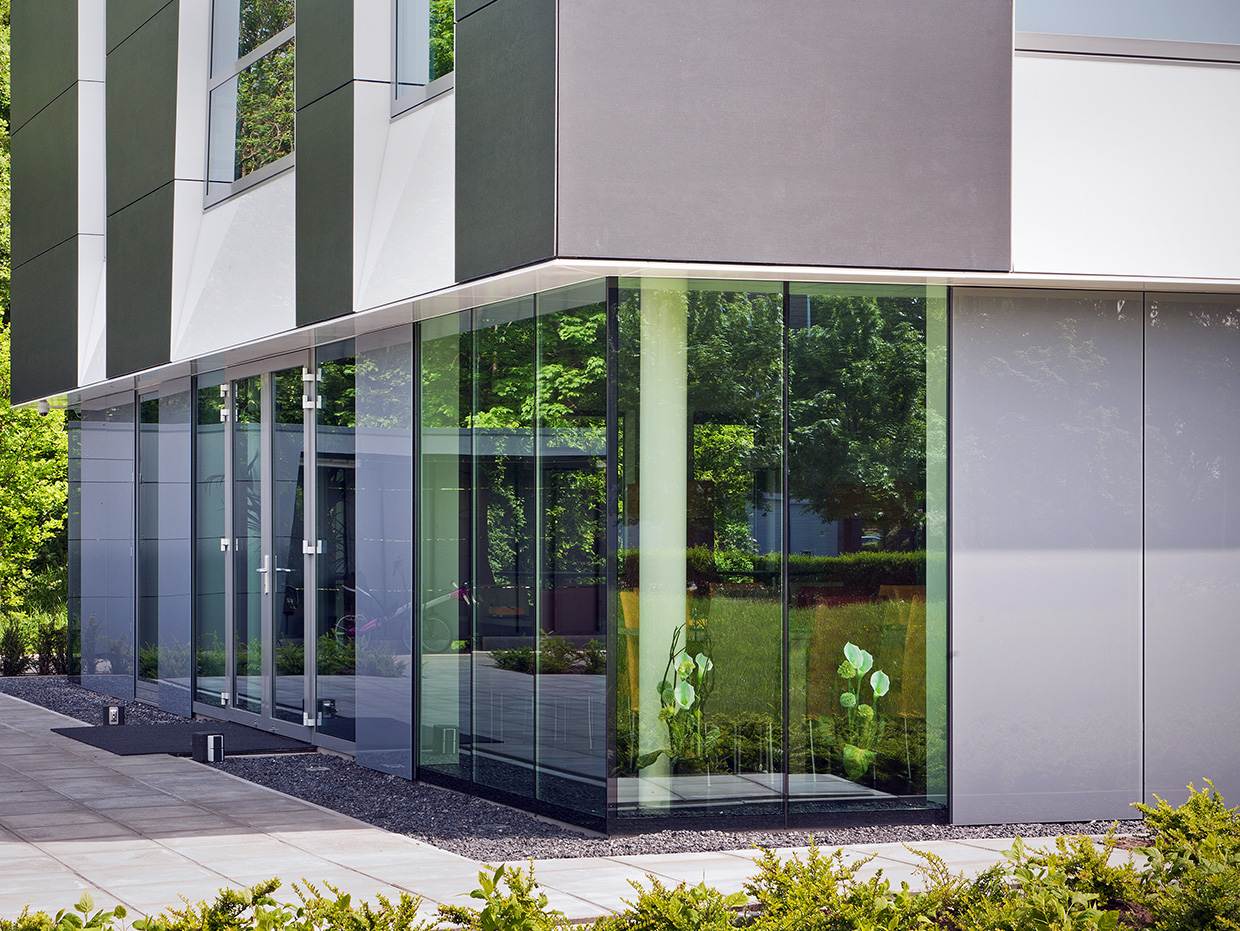
Facing the challenge together
Do you have questions or want to receive more information about how we can help your organization successfully implement a Lean transformation? If so, please fill out the contact form. One of our Lean experts will then contact you. We look forward to answering your questions and discussing how we can support your organization in achieving lasting improvements.