Problem Solving
Realizing a logistics breakthrough using Lean
We do things the way we’ve been doing them for years…. And at the same time, we know very little about exactly what colleagues, who have also been working in the same process for years, are actually doing. Customers expect ever faster delivery and managements want ever more efficient work. But how are we going to make that happen? Our Lean Black Belts are able to realize breakthroughs in this. First, it is made clear which process and which department is involved. Then the value stream is mapped out together with the team. This can be done for example with a Spaghetti diagram, Makagami (Brown paper) or Value Stream Map. If historical data is present, we apply Process Mining. It is always interesting to see that by applying these types of techniques, it suddenly becomes clear how processes actually run. The Lean Black Belt is able to come up with solutions in both office and industrial environments. The solution is often found in a different way of working. Determining this different way of working together with the employees requires change management skills. Sometimes automation is the solution. Consider ‘Robotic Process Automation’ (RPA), a way of having repetitive manual processes performed by a robot (software tool).
Making a technical breakthrough using Six Sigma
Sometimes problems are very persistent and there is a lot of downtime or customer complaints. The experts within the organization have already tried various things, but the problem keeps coming back. “How could an outside person solve this problem when our own experts can’t figure it out themselves?” And yet our experienced Lean Six Sigma Black Belts show time and time again that they do manage to achieve a breakthrough.
That’s because they approach the (often technical) problem in a completely different way. The structured Six Sigma DMAIC roadmap is the project-based approach they take. In it, they look primarily at the data that can be linked to the process or problem. This data-driven approach really works! In doing so, the Six Sigma Black Belt draws on a huge toolbox of data science techniques. Think ‘Measurement System Analysis’ (MSA), ‘Design of Experiments’ (DOE), ‘Reliability Analysis’ or ‘Predictive Analytics’ (CART, MARS, Random Forests and TreeNet). The only requirement is that data is present or can be collected.
Of course, the Black Belt does not do this alone. After all, he has limited product knowledge, and this is an essential component in a breakthrough project. Therefore, the Black Belt will form a team with experts from the organization itself. These may be people from R&D, process engineering or shop floor employees.
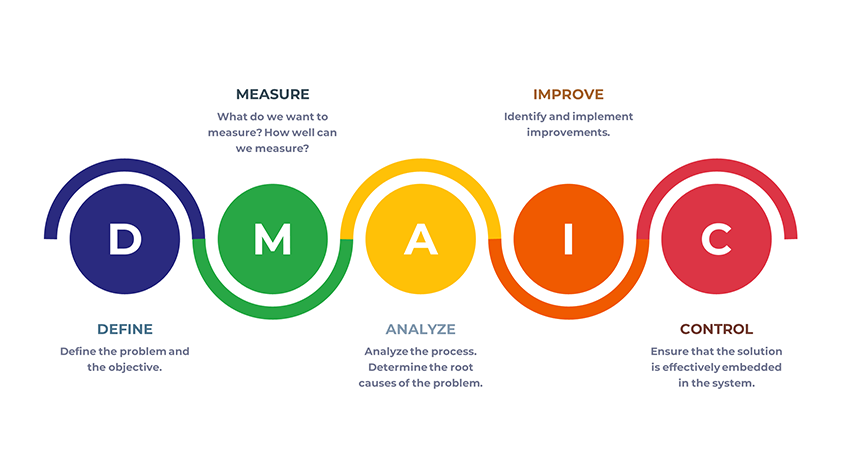
Problem Solving at DSM
Our success story at DSM illustrates the impact of targeted problem-solving techniques within an industrial environment. Our methodology led to significant improvements that not only yielded financial gains, but also increased operational efficiencies.
Results:
✅ Cost savings of 750,000 euros.
✅ Turnaround time shortened by 40%.
✅ More peace and clarity within the organization.
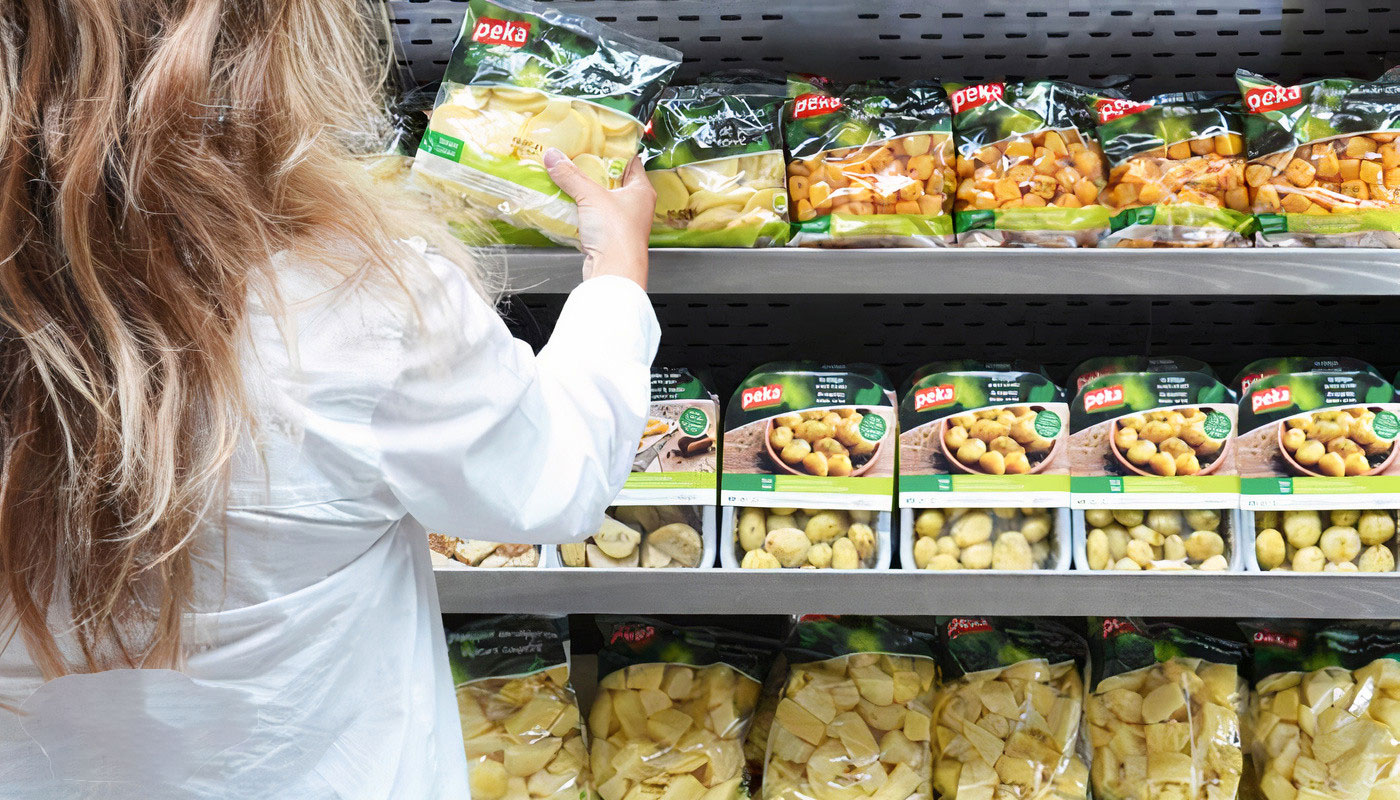
Increased production and reduced water consumption at Peka Kroef
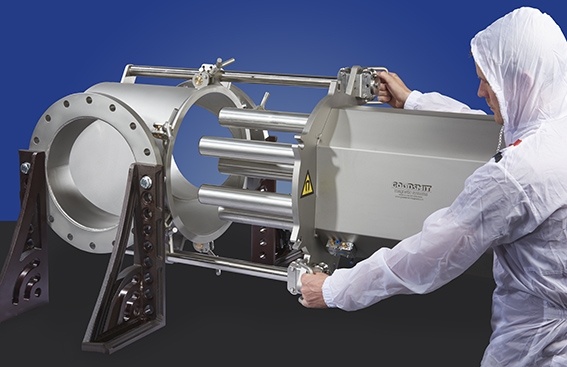
More than 90% First Time Right at Goudsmit
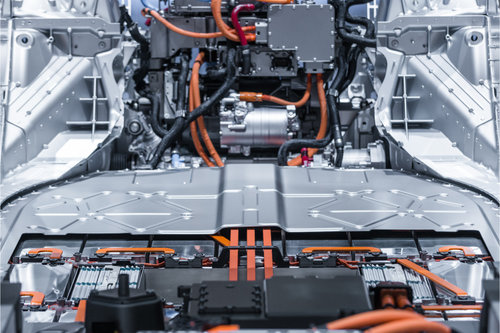
Sensata ensures quality with Design for Six Sigma
people certified in Lean Six Sigma
elevated organizations to a higher level
years of lasting impact
Improve your organization with Problem Solving
Realize lasting improvements and tackle complex challenges with our structured problem-solving methods. Our approach enables your organization to effectively address both significant and subtle bottlenecks. Through this approach, your team will learn not only to identify and solve problems, but also to implement preventive measures that help achieve financial and operational goals.
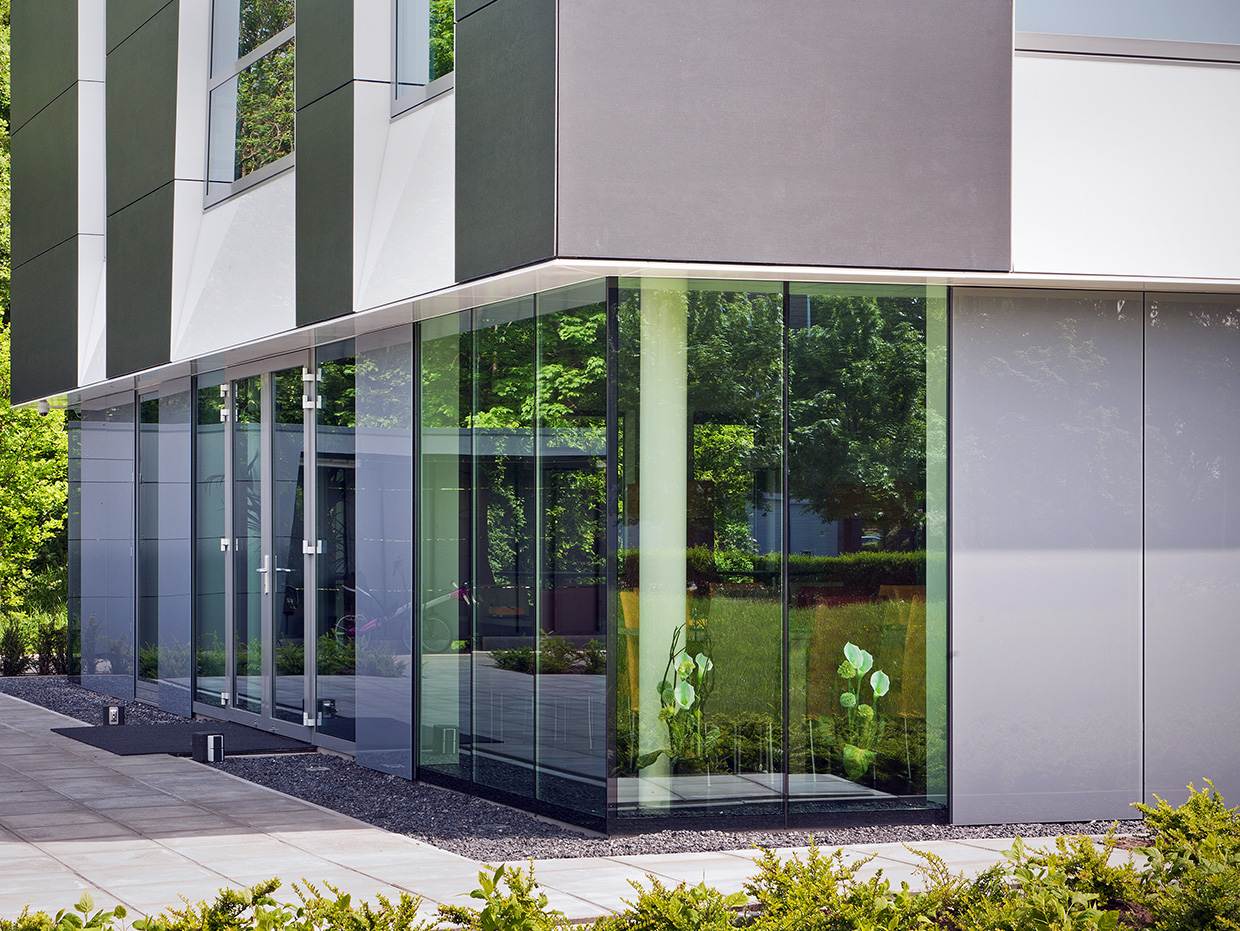
Coming to a solution together
Do you have questions or want to receive more information about how we can help your organization solve problems effectively? If so, please fill out the contact form. One of our troubleshooting experts will contact you. We look forward to answering your questions and discussing how we can support your organization in achieving lasting improvements.